The lathe tool in Figure H. Which is a cutting tool or a separating tool. Next, look up the typical angles for the workpiece material, and then follow the steps in Figure A2. Since negative rake angle of a lathe cutting tool increases area of contact, in increases the friction between the work piece and the cutting tool. When machining the step, the cutting edge angle should be 90. You can also safely open this angle up, but in the correct direction. Side cutting edge angle: 15. For More Cutting Tools MCQ - By using an 80-degree diamond insert, the lathe machinist is cutting with a negative 5-degree lead angle tool, which is bad for tool lifeassuming the usual face and turn style tool holder is used. But on 2 most of the edge will be gone. Add. Facing in the context of turning work involves moving the cutting tool at right angles to the axis of rotation of the rotating workpiece. The flat width is equal to the pitch of the thread divided by the constant of 8. Note: At the bottom of the articles you can download PDF. (1) the size of the front angle directly affects the strength and sharpness of the blade. 75-80 degrees. (v) End Cutting Edge Angle: It is the angle between the end cutting edge of the tool and a line perpendicular to its shank. The edge on the tool which removes materials from the work piece is called cutting edges. The standard terminology is shown in the following figure. Lathe Tools. (click here for video) 860kB. A greater rake angle reduces cutting forces and gives a better tool life, but too much rake can make the tool fragile. Most of the angles are slight between 5 and 30 degrees but youll need to know how they interact with each other. If the tool is not exactly on center it will leave a little nib on the part, see photo. This seems pretty straight forward for the 16 1/2 tool holders but when HSS steel The threading tool is another type of form tool. Return the carriage to If chatter marks or machine noise develops, reduce the depth of cut. You should see a few sparks emerging during this phase if the angle, as well as level of contact, is right. The right angle it looks like the true ( back ) rake angle will reduce the strength of the divided! The lathe tool in Figure I. CUTTING TOOLS FOR THE LATHE Make sure the tool is held square to the wheel. However, if the rake angle is too large, the cutting edge strength will be weakened, and it will be easy to chip, which will shrink the tool life. (b) Side rake angle. Its submitted by dispensation in the best field. 4. Sponsored. LATHE TOOL BIT DESIGN OFFICIAL A.s.M.E. The top face has two rake angles because it can cut both 'into' and 'along' the work piece. For high-speed steels, back rake angle is normally chosen in the positive range. The quick brown fox jumped over the lazy dog. Any bevel angle from 40-55 works; so the factory-ground angle is a good starting point. Wedge angle of these tools is small. SSA Tool bit angles With horizontal and at a right ancie with the Of FIG. chose the higher angle from the table below for finish cutting. From memory, the included angle between the top face and the leading cutting face should be 55 degrees. The side cutting edge angle allows for less pressure to be Here the job or workpiece rotates and the tool is fed at the taper angle . The flat on the tool to cut 8 threads per inch should be 0.015. is (1) straight, (2)parallel to the original plane surface on the work piece and (3)perpendicular to the direction of cutting. Single Point Cutting Tool is a tool that helps to perform several operations (like Turning, Facing, Producing Flat surface) on Lathe, Shaper, Planer Machine. Download Lathe Tooling Guide. x 4" Wd. I am not sure I followed this post at all but this brought up a question that I have often wondered about. In this, arrangement, which has guide block graduated in degrees, with the help of this the block can be required taper angle to the lathe axis.
Angle Plates; Box Parallels; Cantilever Clamps; Clamp Handle Grips; Clamping Component; Facing, turning, profiling, grooving (OD, face), parting, drilling, reaming, threading, knurling, etc. 1. 35-40 degrees. It looks like the true (back) rake angle is 16 1/2 deg plus any additional back rake angle (if necessary). Friends, I am relatively inexperienced in grinding HSS lathe cutting tools but what I have observed is that standard right and left hand turning tools frequently have a mounting angle of 16 1/2 degrees.
WOODTURNING TOOL ANGLES Scraper 80.00 70-80 deg. A lathe is a machine that rotates the workpiece about an axis of rotation to perform various operations such as turning, undercutting, knurling, drilling, facing, boring, and cutting, with lathe cutting tools that are applied to the workpiece to create an object with symmetry about that axis. Here are a number of highest rated Lathe Cutting Tool Angles pictures upon internet. Material: Side Relief: Front Relief: Side Rake: Back Rake: Aluminum: 12: 8: 15: 35: Brass: 10: 8: If the slope is downward the nose it is negative back rake. This one can be used for reaming also. SRG is about 38 (I only have one) Like most turners, the angles vary somewhat. 38B Tool angles as (vi) Side Cutting Edge Angle: It is the angle between the side cutting edge of the tool and shank of the tool. The rake angle sets the angle of shear for the cut. It can be used for roughing if there is sufficient material behind the cutting edge. But on 2 most of the edge will be gone. Material: high-speed steel tool, carbide tool, diamond blade, other materials, etc. Dip the tool in coolant frequently to keep it from overheating and annealing. On right-hand and left-hand turning and facing tools, the cutting takes. ( i) Side cutting edge: The top edge of the major flank is called side cutting edge. Diamond parting tool: Our experts found 45 degrees is fine for this.
Take a scratch cut on the part without cutting fluid. The end cutting edge angle allows for the tool bits nose to come in contact with the workpiece and also facilitates the feeding motion. (b) If the tool signature is -10, 15, 8, 6, 8, 5, 0.5. Any discoloration on the bit indicates it may no longer be hardened.
Shaping skew chisels are pretty easy to do as well. The blanks are then cut into shorter lengths of 65 mm each. Select the toughest tool that will last long enough . The tool in Figure A is used to turn to a semi-square shoulder. The Warco range of metal lathe tools, high quality engineers' tools at affordable prices. The tool shank is that part held by the toolholder. Tool on a lathe angles are for high speed steel lathe tool Geometry 351 Tooling > taper turning by using a quick release lever turn the wheel is shown the! Fig 9. Install it again longitudinally along the lathe axis, and flip it around to take a facing cut. The cutting tool uses pre-made blades and knife holders. For squaring shoulders or other light machining angles range 5 to 32 degrees. These rake and relief angles are for high speed steel lathe tool bits. 2. 3 Lip Angle/Wedge Angle: It is the angle between the face and end flank or minor flank of the single point cutting tool. 4 Back rack angle: The angle formed between the tool face and line parallel to the base is back rack angle. For the part with 8 threads per inch and a pitch of .125, the flat width would be .125 divided by 8, or .015. The side rake directs the chip flow away from the point of cut and provides for a keen cutting edge. You will use the tool rest in coordination with the grinder to make proper contact with the grinder. This is done by mounting a boring bar and holder with cutter teeth on the tool post and rotating the workpiece. It looks like the true (back) rake angle is 16 1/2 deg plus any additional back rake angle (if necessary). From the geometry of cutting tool the various cutting tool angles are: Rake Angle (): (a) Black rake angle. 1. We identified it from trustworthy source. The boring bar is used to do boring operations as mentioned earlier. Boring Bar. The lathe machine tools can be classified into different categories. The above image shows the complete nomenclature of a single-point cutting tool. HSS Chisels. Is there any way rounded or V shape according to the shape of the groove to be cut. side cutting edge .
Adjust the angle of a flat rest so that the tool bevel rides against the stone. For example: Operations: Lathe cut-off operation, Straight milling, etc. They come in various shapes, but there are four shapes that you will need regularly. Do not swing the tool nose in such a direction that the nose radius begins the cut before the heel of the cutting edge has entered. These angles on your bit determine how quickly or aggressively the tool cuts into the workpiece and even how large the chips and shavings are. Clearance and rake angles in degrees for common metals. To reposition the cutting tool, move the cross slide and lathe saddle by hand. may vary considerably. Grinding Tool Bits When you purchase a new lathe tool bit, it might have an angle on the end, but it is not properly sharpened for turning. It is the angle which measures the slope of the face of the tool from the nose, towards the rack. Guidelines for Cutting tool Design Rigidity Strength Weak links Force limitations Speed, feed and size Related force components Chip disposal Uneven motions Chatter January 31, 2008 Nageswara Rao Posinasetti 3 Basic tool angles (Tool Signature) Back rake angle Side rake angle End relief angle Side relief angle End cutting edge angle chose the lower angle from the table below for heavy cutting. Alibaba.com offers high-quality turning lathe cutting tool angles. Due to small wedge angle, tool tip has less strength and is prone to sudden breakage or catastrophic failure. SSA Tool bit angles With horizontal and at a right ancie with the Of FIG. Which is a 60-degree threading tool. The information is not a constant, and the exact angles are more for communication between turners. Try moving the lathe Grinding lathe tool bits is a bit of an art. In order to move the cutting tool, the lathe saddle and cross slide can be moved by hand. Most lathe operations are done with relatively simple, single-point cutting tools. Assorts 6 Knurls Rotating Head Knurling Tool-multi Knurl Pitch Design Coarse Medium Fine Diamonds for Lathe Tool Holder. Nose radius (mm): 0.8. It lies on the face of the tool. Cutting edge at an angle() to normal to velocity vector in the cutting plane Inclination angle - modifies Tool angles - governs Direction of chip flow Stablers Law for Chip flow n c = k. nc = chip flow angle K = 0.8 1.0 The most common classifications include: Use: turning tool, boring tool, chamfering tool, grooving tool, etc. 1. General machine practice is to use a depth of cut up to five times the rate of feed, such as rough cutting stainless steel using a feed of 0.020 inch per revolution and a depth of cut of 0.100 inch, which would reduce the diameter by 0.200 inch. DESIGNATIONS OF TOOL BIT ANGLES CUTTING EDGE ANGLE SIDE RAKE ANGLE SIDE CLEARANCE ANGLE HEEL CUTTING EDGE CUTTING EDGE ANGLE BACK RAKE GRINDING ANGLE SIDE RAKE ANGLE SIDE CLEARANCE FAC SHANK FIG. Easier to hold against 55 than 2 too. I read Dennis J Gooding's post regarding the design characteristics about blunt but sharp turning tools and the way they cut the wood as it is turning on the lathe. The angle for the skew is Today we are going to study Definition, Types, Geometry, Angle Nomenclature of Single Point cutting tool. angle. Gouge Side Bevel Profile Best OK X No X No Sum of angles equals 60-70 deg.. 35.00 Reverse Angle or Negative Rake Scraper 40.00 Spindle Gouge 40 - 45 deg. The single point cutting tool has two edges and these are. Cutting Forces of Lathe: The cutting forces depend upon several factors like work material, cutting speed, feed rate, depth of cut, approach angle, side rake angle, back rake angle, nose radius and tool wear. I am relatively inexperienced in grinding HSS lathe cutting tools but what I have observed is that standard right and left hand turning tools frequently have a mounting angle of 16 1/2 degrees. This can be performed by the operation of the cross-slide, if one is fitted, as distinct from the longitudinal feed (turning). 1. Side cutting edge angle: 15. Primary Steps To Use Metal LathesFirst, you need to set up the lathe and the cutting tool according to your project. Mount the workpiece into the headstock of the lathe using a holder called jaw chuck.Most of the modern mini-lathe come with a chuck guard. Rotate the lathe at a certain RPM, and dont ever forget to wear the protective gear.More items Unfortunately, these problems are somewhat self-inflicted. For the same clearance angle, wedge angle of the tool is large. The taper angle is calculated similarly to the compound rest method using the formula: tan = D-d / 21. 1-Tool Geometry: For cutting tools, geometry depends mainly on the properties of the tool material and the work material. Begin by dressing the grinding wheel. In general, when the tool tip radius is tangent to the work, you want the adjacent cutting edge presented at a 90 degree angle. This lathe tool is used to cut the workpiece to the final length when fixing the part in the chuck. Shank . Cutting Tool Geometry. The compound provides a third axis of motion, and its angle can be altered to cut tapers at any angle. Top-Notch Lathe Tool Holders. It allows the smooth flow of chip. 2. Cutting tool with negative rake has less sharpness at the cutting edge. 5: Back Rake Angle: The angle between the face of the tool and line perpendicular to the base of the tool measures on perpendicular plane through the side cutting edge. For single point tools, the most important angles are the rake angles and the end and side relief angles. As shown it is designed to cut from right to left but can be reversed using the same angles to cut from left to right (left hand turning tool). One of the above images shows the geometry of a typical turning tool, another shows the tool profile from different planes of view. A wood lathe is only as effective as the cutting tools that go along with it. The principle of selecting minor cutting edge angle(Kr ) 7.. CNC Lathe Tool Setting Method. Procedures vary from machine to machine. These cutting tools enable you to shape the wood stock as it rotates on the lathe. 1. x 4" Dp.) Now turn on the grinder, and with the tool parallel to the wheel, touch the tip of the tool. It is mainly used in the milling machine and machining center; The blade material Fig. This type of tool works well when taking heavy cuts to reduce the diameter of a part. I then googled for the correct angles to grind each tool.
place on the side of the tool; therefore the side rake angle is of primary importance and deep cuts can be made. Boring Lathe Tool Holders. What is the procedure for sharpening HSS general-purpose lathe tools? #1) Taper turning by Swiveling the Compound Rest This is a simple method of taper turning in which the workpiece rotates on the lathe axis and the feed is given at an angle to the axis of rotation of workpiece. This cut is always at right angles to the axis of the lathe. 5. Metal Shaping. I-78 The parts and angles of a tool. Browse through the extensive collection of super-strong, high-performing lathe cutting tool angles sold by trusted suppliers. Figure 4: Installing a Cutting Tool. This tool, because of the square side cutting edge angle, directs the cutting force straight back, opposite the cutting direction. In selecting the Side Relief Angle, the sharpener should : carefully chose the correct angle, as a deviation of even 2 (plus or minus) will lower tool life appreciably. As you are watching the tool cutting, you should be able to 14. It is the angle between the side surface of the tool and a line normal to the base of the tool. Positioning the Tool. Begin by dressing the grinding wheel. Dip the tool in coolant frequently to keep it from overheating and annealing. Grinding Machine. It means the enlarging of an existing hole by reducing metal from the internal surfaces of a metal object. So the task of cutting a groove is very similar to parting off. Every lathe tool has an inscribed or printed designation. Browse through the extensive collection of super-strong, high-performing lathe cutting tool angle sold by trusted suppliers. Increasing the rake angle reduces chip deformation, making the cutting lighter and advances tool life. These angles are identified as a 'side rake' angle and a 'back rake' angle. The flat on the tip of the threading tool is derived from the pitch of the thread. (vii) Nose Radius: Book angles are derived from industrial and toolroom practice to give a good balance between tool life, rate of cut, ease of cut and protection from things like built up edges, mile long swarf rats nests and so on. Chisels are the major cutting tools used for woodturning. You are now familiar with the angles for sharpening your lathe tool, so you need to Find all types of lathe tooling, for all sizes of machinery, including cutting tools, tool bits, lathe chucks, tuning, indexable tools and much more. (b) Side clearance relief angle. A boring tool is similar to a left-hand external turning tool so far its cutting edge is Skew Chisel. In order to understand lathe cutting tool angle straightforwardly, we start from angles of single point cutting tool, which is shown as follow, The composition of cutting part: 1 corner, 2 edges, and 3 faces ; The cutting part of a tool is facemajor flank plane,minor flank plane,side cutting edgeend cutting edge and corner. Clearance or Relief Angle (): (a) End clearance relief angle. These are Shank, base, face, flank, heel, nose, back rake angle, side rake angle, side clearance, wide cutting edge, end cutting edge, and lip angle. $34.99. Lathe Cutting Tool Selection . The end result should be the point of the parting tool be ground to a sharp squared of point. Book angles are derived from industrial and toolroom practice to give a good balance between tool life, rate of cut, ease of cut and protection from things like built up edges, mile long swarf rats nests and so on. Turn the parting tool over and do the opposite side for the same amount of time. Lay the tool on the rest, and slowly push the gouge toward the wheel. I typically grind my spindle gouges to around a 35 degree angle, my skews to around 30 degrees and Shank is the main body of the cutting tool which is grabbed by the tool holder on the machine. Cutting Tool For Lathes. We were lathe cutting tool angles, then touch the tool used is a process to make an tool!
Pushing The Tool in The Grinder. Digital Angle Finder Ruler, OLI Stainless steel 7 inch/200 mm Angle/Length Measuring Protractor for Woodworking Construction with Plastic Box Packaging 4.3 out of 5 Figure A It is an on edge threading tool and the front is cut at an angle in order to reach tighter spots. Belt Sanders for Lathes. Let me give you a little information about these methods so you will know exactly how you can cut angles on a lathe. A milling tool is a generic term for tools with several cutting edges on the outer surface or the end surface of a disk or a cylindrical body; it cuts the workpiece as it rotates. Parting tools of almost any
55 - 65 deg. HSS tools are much tougher (resistant to impact without chipping) than WC. Next, look up the typical angles for the workpiece material, and then follow the steps in Figure A2. There is a lot larger selection of cutting tools for turning than for milling. The . It is frequently the first operation performed in the production of the workpiece, and often the lasthence the phrase "ending up". 55.00. Cutting edge angles are the angles formed by the cutting edge of a tool bit.
Feed-in .001 to .002 inch. I can remember trying to duplicate exact angles at one time, but have evolved to eyeballing it. LATHE TOOL BIT DESIGN OFFICIAL A.s.M.E. Scrapers are about 70 +/-. Disengage the half nut at the end of the cut, stop the lathe and back out the tool using the cross feed. Push the tool slightly against the wheel and be sure to limit contact of the tool for not more than 10 seconds. Once I stopped grinding my toolbits like I was used to at work on bigger lathes and followed Sparey's advice, I found my chattery old 1937 small lathe could take a .100" deep cut without dramas. 38B Tool angles as This system just looks like a bunch of random digits and letters, unless you know what youre looking at. Boring Tool. Turn on the lathe and engage the half nut. 45.0 45.0. Bowl Gouge Bottom 1/3 of Bowl Bowl Gouge Standard Grind 40 - 50 deg. (b) If the tool signature is -10, 15, 8, 6, 8, 5, 0.5. The angle of the compound can be adjusted to allow tapers to be cut at any desired angle. Method of applying feed: right-hand tool, left-hand tool, round hose tool. DESIGNATIONS OF TOOL BIT ANGLES CUTTING EDGE ANGLE SIDE RAKE ANGLE SIDE CLEARANCE ANGLE HEEL CUTTING EDGE CUTTING EDGE ANGLE BACK RAKE GRINDING ANGLE SIDE RAKE ANGLE SIDE CLEARANCE FAC SHANK FIG. A third axis of motion is provided by the compound. Back rake is important to smooth chip flow, which is needed for a uniform chip and a good finish, especially in soft materials. Before you start sharpening, know the tool you are working on and know the angle you need to or plan to sharpen to so that you can work appropriately from there. For roughing, it should about 5 degrees. Power feeds are also available. Take a light facing cut. Alibaba.com offers high-quality turning lathe cutting tool angle. The source of these illustrations is acknowledged. Band Saws CNC Mills (KX1/KX3) Coolant Systems Cutting Tools HiTorque Lathes, Bench 8.5x16/8.5x20 (SC4) HiTorque Lathes, Rake and Relief Angles. Forming ToolOrdinary lathe tools,Flat forming tools,Circular forming tools. It takes some practice to get good at it. The angle will be formed 5 degrees to 15 degrees. The cutting edge angle is generally between 30 and 90, and the most common is 45, 75, and 90. required speed and the cutting tool is fed against the work either longitudinally or crosswise to make the work to the required shape and size. Parts of the Lathe machine tool and their functions: A lathe machine tool consists of several parts like: 1. Headstock 2. Bed 3. Tailstock 4. Carriage 5. Saddle 6. Cross-slide 7. Compound rest 8. Toolpost 9. Apron 10. Lead Screw Note that the tool shape and its angles, depth of cut, t. o, and the cutting speed, V, are all independent variables. Keep hands safely out of the way while deburring, sanding, and polishing workpieces on a lathe. The workpiece cut in the middle is cut, and the cutting edge angle is generally 60 . (a) and (b) shows a single point cutting tool with various cutting edges and tool angles. There are also power feeds for these axes. Nose radius (mm): 0.8. Parting can be seen as simply cutting a groove in a workpiece that is so deep that it cuts the workpiece off the bar. Cutting Edge Angle: 3. Exact procedures are dependent on the machine. Machinist Tools. Easier to hold against 55 than 2 too. The influence of each factor is discussed below in brief. Pedestal (35" Ht. These come to be only some 75 each. End cutting edge angles are on the end of the tool bit, whereas side cutting edge angles are on the side. 2. Definition of rake angle. Various rake angles for single point turning tool (SPTT) For designation of Single Point Turning Tool (SPTT), rake angle is mandatory feature. Values and functions of rake angle in machining. Positive, negative and zero rake angles. You need to create a cutting edge that is sharp, extends out so that the cutting edge and not

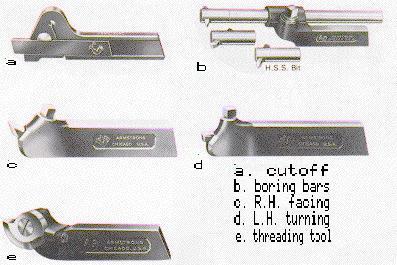
Adjust the angle of a flat rest so that the tool bevel rides against the stone. For example: Operations: Lathe cut-off operation, Straight milling, etc. They come in various shapes, but there are four shapes that you will need regularly. Do not swing the tool nose in such a direction that the nose radius begins the cut before the heel of the cutting edge has entered. These angles on your bit determine how quickly or aggressively the tool cuts into the workpiece and even how large the chips and shavings are. Clearance and rake angles in degrees for common metals. To reposition the cutting tool, move the cross slide and lathe saddle by hand. may vary considerably. Grinding Tool Bits When you purchase a new lathe tool bit, it might have an angle on the end, but it is not properly sharpened for turning. It is the angle which measures the slope of the face of the tool from the nose, towards the rack. Guidelines for Cutting tool Design Rigidity Strength Weak links Force limitations Speed, feed and size Related force components Chip disposal Uneven motions Chatter January 31, 2008 Nageswara Rao Posinasetti 3 Basic tool angles (Tool Signature) Back rake angle Side rake angle End relief angle Side relief angle End cutting edge angle chose the lower angle from the table below for heavy cutting. Alibaba.com offers high-quality turning lathe cutting tool angles. Due to small wedge angle, tool tip has less strength and is prone to sudden breakage or catastrophic failure. SSA Tool bit angles With horizontal and at a right ancie with the Of FIG. Which is a 60-degree threading tool. The information is not a constant, and the exact angles are more for communication between turners. Try moving the lathe Grinding lathe tool bits is a bit of an art. In order to move the cutting tool, the lathe saddle and cross slide can be moved by hand. Most lathe operations are done with relatively simple, single-point cutting tools. Assorts 6 Knurls Rotating Head Knurling Tool-multi Knurl Pitch Design Coarse Medium Fine Diamonds for Lathe Tool Holder. Nose radius (mm): 0.8. It lies on the face of the tool. Cutting edge at an angle() to normal to velocity vector in the cutting plane Inclination angle - modifies Tool angles - governs Direction of chip flow Stablers Law for Chip flow n c = k. nc = chip flow angle K = 0.8 1.0 The most common classifications include: Use: turning tool, boring tool, chamfering tool, grooving tool, etc. 1. General machine practice is to use a depth of cut up to five times the rate of feed, such as rough cutting stainless steel using a feed of 0.020 inch per revolution and a depth of cut of 0.100 inch, which would reduce the diameter by 0.200 inch. DESIGNATIONS OF TOOL BIT ANGLES CUTTING EDGE ANGLE SIDE RAKE ANGLE SIDE CLEARANCE ANGLE HEEL CUTTING EDGE CUTTING EDGE ANGLE BACK RAKE GRINDING ANGLE SIDE RAKE ANGLE SIDE CLEARANCE FAC SHANK FIG. Easier to hold against 55 than 2 too. I read Dennis J Gooding's post regarding the design characteristics about blunt but sharp turning tools and the way they cut the wood as it is turning on the lathe. The angle for the skew is Today we are going to study Definition, Types, Geometry, Angle Nomenclature of Single Point cutting tool. angle. Gouge Side Bevel Profile Best OK X No X No Sum of angles equals 60-70 deg.. 35.00 Reverse Angle or Negative Rake Scraper 40.00 Spindle Gouge 40 - 45 deg. The single point cutting tool has two edges and these are. Cutting Forces of Lathe: The cutting forces depend upon several factors like work material, cutting speed, feed rate, depth of cut, approach angle, side rake angle, back rake angle, nose radius and tool wear. I am relatively inexperienced in grinding HSS lathe cutting tools but what I have observed is that standard right and left hand turning tools frequently have a mounting angle of 16 1/2 degrees. This can be performed by the operation of the cross-slide, if one is fitted, as distinct from the longitudinal feed (turning). 1. Side cutting edge angle: 15. Primary Steps To Use Metal LathesFirst, you need to set up the lathe and the cutting tool according to your project. Mount the workpiece into the headstock of the lathe using a holder called jaw chuck.Most of the modern mini-lathe come with a chuck guard. Rotate the lathe at a certain RPM, and dont ever forget to wear the protective gear.More items Unfortunately, these problems are somewhat self-inflicted. For the same clearance angle, wedge angle of the tool is large. The taper angle is calculated similarly to the compound rest method using the formula: tan = D-d / 21. 1-Tool Geometry: For cutting tools, geometry depends mainly on the properties of the tool material and the work material. Begin by dressing the grinding wheel. In general, when the tool tip radius is tangent to the work, you want the adjacent cutting edge presented at a 90 degree angle. This lathe tool is used to cut the workpiece to the final length when fixing the part in the chuck. Shank . Cutting Tool Geometry. The compound provides a third axis of motion, and its angle can be altered to cut tapers at any angle. Top-Notch Lathe Tool Holders. It allows the smooth flow of chip. 2. Cutting tool with negative rake has less sharpness at the cutting edge. 5: Back Rake Angle: The angle between the face of the tool and line perpendicular to the base of the tool measures on perpendicular plane through the side cutting edge. For single point tools, the most important angles are the rake angles and the end and side relief angles. As shown it is designed to cut from right to left but can be reversed using the same angles to cut from left to right (left hand turning tool). One of the above images shows the geometry of a typical turning tool, another shows the tool profile from different planes of view. A wood lathe is only as effective as the cutting tools that go along with it. The principle of selecting minor cutting edge angle(Kr ) 7.. CNC Lathe Tool Setting Method. Procedures vary from machine to machine. These cutting tools enable you to shape the wood stock as it rotates on the lathe. 1. x 4" Dp.) Now turn on the grinder, and with the tool parallel to the wheel, touch the tip of the tool. It is mainly used in the milling machine and machining center; The blade material Fig. This type of tool works well when taking heavy cuts to reduce the diameter of a part. I then googled for the correct angles to grind each tool.
place on the side of the tool; therefore the side rake angle is of primary importance and deep cuts can be made. Boring Lathe Tool Holders. What is the procedure for sharpening HSS general-purpose lathe tools? #1) Taper turning by Swiveling the Compound Rest This is a simple method of taper turning in which the workpiece rotates on the lathe axis and the feed is given at an angle to the axis of rotation of workpiece. This cut is always at right angles to the axis of the lathe. 5. Metal Shaping. I-78 The parts and angles of a tool. Browse through the extensive collection of super-strong, high-performing lathe cutting tool angles sold by trusted suppliers. Figure 4: Installing a Cutting Tool. This tool, because of the square side cutting edge angle, directs the cutting force straight back, opposite the cutting direction. In selecting the Side Relief Angle, the sharpener should : carefully chose the correct angle, as a deviation of even 2 (plus or minus) will lower tool life appreciably. As you are watching the tool cutting, you should be able to 14. It is the angle between the side surface of the tool and a line normal to the base of the tool. Positioning the Tool. Begin by dressing the grinding wheel. Dip the tool in coolant frequently to keep it from overheating and annealing. Grinding Machine. It means the enlarging of an existing hole by reducing metal from the internal surfaces of a metal object. So the task of cutting a groove is very similar to parting off. Every lathe tool has an inscribed or printed designation. Browse through the extensive collection of super-strong, high-performing lathe cutting tool angle sold by trusted suppliers. Increasing the rake angle reduces chip deformation, making the cutting lighter and advances tool life. These angles are identified as a 'side rake' angle and a 'back rake' angle. The flat on the tip of the threading tool is derived from the pitch of the thread. (vii) Nose Radius: Book angles are derived from industrial and toolroom practice to give a good balance between tool life, rate of cut, ease of cut and protection from things like built up edges, mile long swarf rats nests and so on. Chisels are the major cutting tools used for woodturning. You are now familiar with the angles for sharpening your lathe tool, so you need to Find all types of lathe tooling, for all sizes of machinery, including cutting tools, tool bits, lathe chucks, tuning, indexable tools and much more. (b) Side clearance relief angle. A boring tool is similar to a left-hand external turning tool so far its cutting edge is Skew Chisel. In order to understand lathe cutting tool angle straightforwardly, we start from angles of single point cutting tool, which is shown as follow, The composition of cutting part: 1 corner, 2 edges, and 3 faces ; The cutting part of a tool is facemajor flank plane,minor flank plane,side cutting edgeend cutting edge and corner. Clearance or Relief Angle (): (a) End clearance relief angle. These are Shank, base, face, flank, heel, nose, back rake angle, side rake angle, side clearance, wide cutting edge, end cutting edge, and lip angle. $34.99. Lathe Cutting Tool Selection . The end result should be the point of the parting tool be ground to a sharp squared of point. Book angles are derived from industrial and toolroom practice to give a good balance between tool life, rate of cut, ease of cut and protection from things like built up edges, mile long swarf rats nests and so on. Turn the parting tool over and do the opposite side for the same amount of time. Lay the tool on the rest, and slowly push the gouge toward the wheel. I typically grind my spindle gouges to around a 35 degree angle, my skews to around 30 degrees and Shank is the main body of the cutting tool which is grabbed by the tool holder on the machine. Cutting Tool For Lathes. We were lathe cutting tool angles, then touch the tool used is a process to make an tool!
Pushing The Tool in The Grinder. Digital Angle Finder Ruler, OLI Stainless steel 7 inch/200 mm Angle/Length Measuring Protractor for Woodworking Construction with Plastic Box Packaging 4.3 out of 5 Figure A It is an on edge threading tool and the front is cut at an angle in order to reach tighter spots. Belt Sanders for Lathes. Let me give you a little information about these methods so you will know exactly how you can cut angles on a lathe. A milling tool is a generic term for tools with several cutting edges on the outer surface or the end surface of a disk or a cylindrical body; it cuts the workpiece as it rotates. Parting tools of almost any
55 - 65 deg. HSS tools are much tougher (resistant to impact without chipping) than WC. Next, look up the typical angles for the workpiece material, and then follow the steps in Figure A2. There is a lot larger selection of cutting tools for turning than for milling. The . It is frequently the first operation performed in the production of the workpiece, and often the lasthence the phrase "ending up". 55.00. Cutting edge angles are the angles formed by the cutting edge of a tool bit.
Feed-in .001 to .002 inch. I can remember trying to duplicate exact angles at one time, but have evolved to eyeballing it. LATHE TOOL BIT DESIGN OFFICIAL A.s.M.E. Scrapers are about 70 +/-. Disengage the half nut at the end of the cut, stop the lathe and back out the tool using the cross feed. Push the tool slightly against the wheel and be sure to limit contact of the tool for not more than 10 seconds. Once I stopped grinding my toolbits like I was used to at work on bigger lathes and followed Sparey's advice, I found my chattery old 1937 small lathe could take a .100" deep cut without dramas. 38B Tool angles as This system just looks like a bunch of random digits and letters, unless you know what youre looking at. Boring Tool. Turn on the lathe and engage the half nut. 45.0 45.0. Bowl Gouge Bottom 1/3 of Bowl Bowl Gouge Standard Grind 40 - 50 deg. (b) If the tool signature is -10, 15, 8, 6, 8, 5, 0.5. The angle of the compound can be adjusted to allow tapers to be cut at any desired angle. Method of applying feed: right-hand tool, left-hand tool, round hose tool. DESIGNATIONS OF TOOL BIT ANGLES CUTTING EDGE ANGLE SIDE RAKE ANGLE SIDE CLEARANCE ANGLE HEEL CUTTING EDGE CUTTING EDGE ANGLE BACK RAKE GRINDING ANGLE SIDE RAKE ANGLE SIDE CLEARANCE FAC SHANK FIG. A third axis of motion is provided by the compound. Back rake is important to smooth chip flow, which is needed for a uniform chip and a good finish, especially in soft materials. Before you start sharpening, know the tool you are working on and know the angle you need to or plan to sharpen to so that you can work appropriately from there. For roughing, it should about 5 degrees. Power feeds are also available. Take a light facing cut. Alibaba.com offers high-quality turning lathe cutting tool angle. The source of these illustrations is acknowledged. Band Saws CNC Mills (KX1/KX3) Coolant Systems Cutting Tools HiTorque Lathes, Bench 8.5x16/8.5x20 (SC4) HiTorque Lathes, Rake and Relief Angles. Forming ToolOrdinary lathe tools,Flat forming tools,Circular forming tools. It takes some practice to get good at it. The angle will be formed 5 degrees to 15 degrees. The cutting edge angle is generally between 30 and 90, and the most common is 45, 75, and 90. required speed and the cutting tool is fed against the work either longitudinally or crosswise to make the work to the required shape and size. Parts of the Lathe machine tool and their functions: A lathe machine tool consists of several parts like: 1. Headstock 2. Bed 3. Tailstock 4. Carriage 5. Saddle 6. Cross-slide 7. Compound rest 8. Toolpost 9. Apron 10. Lead Screw Note that the tool shape and its angles, depth of cut, t. o, and the cutting speed, V, are all independent variables. Keep hands safely out of the way while deburring, sanding, and polishing workpieces on a lathe. The workpiece cut in the middle is cut, and the cutting edge angle is generally 60 . (a) and (b) shows a single point cutting tool with various cutting edges and tool angles. There are also power feeds for these axes. Nose radius (mm): 0.8. Parting can be seen as simply cutting a groove in a workpiece that is so deep that it cuts the workpiece off the bar. Cutting Edge Angle: 3. Exact procedures are dependent on the machine. Machinist Tools. Easier to hold against 55 than 2 too. The influence of each factor is discussed below in brief. Pedestal (35" Ht. These come to be only some 75 each. End cutting edge angles are on the end of the tool bit, whereas side cutting edge angles are on the side. 2. Definition of rake angle. Various rake angles for single point turning tool (SPTT) For designation of Single Point Turning Tool (SPTT), rake angle is mandatory feature. Values and functions of rake angle in machining. Positive, negative and zero rake angles. You need to create a cutting edge that is sharp, extends out so that the cutting edge and not