The principle of turning a tapered hole is similar to the external taper turning operation and is completed by rotating the work on a chuck or a faceplate. Whatever material used in lathe machine whether metal or wood is molded first. Here the workpiece rotates and the cutting tool is fed at an angle by swivelled compound rest. If we have most suitably equipped metal lathe then it can be used to produce most solids of revolution, plane surfaces, and screw threads or helices. The basic types of tools are Cutting tools, measuring tools, holding tools, Electrical equipment, Driving tools, and miscellaneous tools. right end. With every cut desired the speed, depth and feed of the lathe machine is changed for precision. Compound rest method or swivelling compound rest method. Feed selector is present on the headstock. The direction of the motion of the tool is called a feed. By holding the workpiece at these three centres the machining operation for each of the surfacecan be completed. Similarly, when the tool is moved from left to the right we get the right-hand thread. A lathe is a machining tool that can rotate metal or wood to the desired shape. The tool is fed parallel to the axis. The depth of cut is given by verticle adjustment of the work provided by the attachment. In this, arrangement, which has guide block graduated in degrees, with the help of this the block can be required taper angle to the lathe axis. Taper Turning. This part of the lathe machine is used to hold cylindrical work piece within it. Operations Done By Holding The Work By A Chuck, 3. The tilting of the workpiece or the job to the required taper angle is achieved by the movement of the tailstock with the help of tailstock set over the screw. The feeding is adopted is affected by the movement of the tailstock spindle. This operation is performed after filing to improve the surface quality of the workpiece.
The commonly used tools are mentioned below: A portal of Engg Lectures, Notes & Software, Machining is manufacturing process that involves removing materials using cutting, Ultrasonic machining is changing the manufacturing industries with its superlative, Machining Operation and Types of Machining Tools, Ultrasonic Machining Process, Working Principles & Advantages. There is a wide range of lathe tools that can be classified according to materials, structures and purposes or uses. In this article we will study what is lathe machine main parts, operations and working. document.getElementById("ak_js_1").setAttribute("value",(new Date()).getTime()); This site uses Akismet to reduce spam. Thanks for sharing this wonderful article. It is the process of making holes in the workpiece by the use of drills. This article includes basic lathe operation and other main operations too. Hey! A small hole is provided on the steel bar, which is supported by Tool Post and the wire is allowed to pass through it. If an engineering student thinks of doing a job in any manufacturing industries, then he or she must have a piece of great knowledge about the lathe machine. The feeding movement is provided by the carriage and the vertical movement of the cutter is arranged in the attachment. To cut the workpieces to the required length. Clamping is also used to work the piece about the axis of rotation with the help of a faceplate, clamps/dogs or collet/chuck. Performing any operation on the lathe is much easier than other machines and learning about this machine is equally easier. The speed of this process is slow. When a cylindrical surface two separate axis of rotation, with the first axis, is offset to the other axis then such a workpiece is machined by the operation called eccentric turning. Turning is the operation of removing the excess material from the workpiece to produce a cylindrical surface to the desired length. Cross slide is mounted on the saddle. Read on to know more about the lathe operations: Lathe is a machine that helps in shaping several material pieces in the desired shapes. Now you can Download the free PDF file from below: Image credit for lathe machine: http://engineering.myindialist.com/2009/working-principle-of-lathe-machine/, Saif M. is a Mechanical Engineer by profession.
The working of the lathe machine changes with every operation and cut desired. A lathe is a machine that rotates the piece on the axis in order to perform various operations like cutting, facing, knurling, deformation and more. A tool bit is a non-rotary cutting tool used in metal lathes, shapers, and planers. Here the taper length obtain is equal to the width of the form tool. Your email address will not be published. This method is adopted for the drilling of regular-shaped workpiece. large size tapers can be easily obtained. Lathe machine are of different types according the types of work performed. This is done to provide a better gripping surface when operated by hands.
Some of the common lathe operations are: This is usually the first step of any lathe operation on the lathe machine. The working of the lathe machine changes with every operation and cut desired. Chamfering is the process of beveling the extreme ends of a workpiece. It consists of a boring bar having a single-point cutting tool that enlarges the hole. There are several lathe cutting tools that help in cutting with the lathe machine. 10. Some common lathe operations are drilling, knurling, turning, facing, grooving, parting, threading, boring, and tapping. It is present at the right-hand side of the lathe. A grooving tool is similar to the parting-off tool. During taper turning the feed is set at an angle to the workpiece. The tool is used is called the reamer, which has multi-plate cutting edges. Chamfering is used in woodworking,glass cutting,architecture, and in CAD, and its also a useful tool for deburring. Keep visiting. For to make the cut deeper the parting tool is pulled out and transferred to the side for the cut and to prevent the tool from breaking. In face grooving, the tool machines groove in the face of the workpiece.
Eccentric Turning. The most commonly used lathes are the woodworking lathes. For the grinding external surface, the work may be revolved between centres or on a chuck. That is it, thanks for reading. These factors should be used carefully so that one can avoid from mishandling and mishaps while performing any kind of lathe operation on a lathe machine. Support is also given from the tailstock end. To obtain the required size of the taper the form tool is fed slowly straight into the workpiece by operating the cross slide perpendicular to the lathe axis. It is made of cast iron. When the threads or helical grooves are formed on the out surface of the workpiece is called external thread cutting. The drill is held in the tailstock and the drilling operation is done by advancing the drill in the workpiece by rotating the handle of the tailstock. Some examples of tools that are often used today are the hammer, the wrench (also called a spanner), saws, shovel, telephone, and the computer. The taper angle is calculated similarly to the. This method is useful for small tapers. This includes speed lathe, engine lathe, tool-room lathe, special-purpose lathe, CNC lathe etc. Compound rest can be swivelled to the required angle .
It is a machining operation that is done to produce flat surfaces at the ends of the workpiece. Nuclear Power Plant Working Principle, Advantages, Disadvantages with Diagram. Great article for lathe machineThanks for sharing this resource article on lathe machine tools. Metal spinning, thermal spraying, woodturning, and metalworking are the common operations performed with a lathe machine. Each lathe operation has its own factors that must be considered before starting work. Chip pan is used to collect the chips that are produced during the lathe operation. It comprises of headstock, tailstock, carriage guideways and other parts. Shoulder Turning. The lathe machine operations are given below : 7 Main differences between brazing and soldering (Simplified), 6 Important Types of Manufacturing Processes [2021]. Lathe machine operations are performed by using special attachments: Milling is the operation of removing metal by feeding the work against a rotating cutter having multiple cutting edges.var asau='8288738383';var cid='8918976548';var pid='ca-pub-9958205674121742';var slotId='div-gpt-ad-theengineerspost_com-leader-4-0';var ffid=1;var alS=1710%1000;var container=document.getElementById(slotId);container.style.width='100%';var ins=document.createElement('ins');ins.id=slotId+'-asloaded';ins.className='adsbygoogle ezasloaded';ins.dataset.adClient=pid;if(typeof window.adsenseNoUnit=='undefined'){ins.dataset.adSlot=asau;} A lathe is a machine tool which is used to rotate a workpiece to perform various operations such as turning, facing, knurling, grooving etc., with the help of tools that are applied to the workpiece. And much more can be done with lathe machine. A taper is the uniform increase or decrease in the diameter of the workpiece and measured along with its length. 2022 The Engineers Post - All Rights Reserved / Contact-, 22 Types of Lathe Machine Operations [Complete Guide], 1. The three jaw of the three jaw chuck is made to move simultaneously but the jaws of the four jaw chuck moves independently. Following are the Lathe machine operations done either by holding the workpiece between centres or by a chuck: Lathe machine operations which are performed by holding the work by a chuck or a faceplate or an angle plate are: The operation which is performed by using special attachments are: Read Also about Lathe Machine:if(typeof ez_ad_units!='undefined'){ez_ad_units.push([[336,280],'theengineerspost_com-box-4','ezslot_4',672,'0','0'])};if(typeof __ez_fad_position!='undefined'){__ez_fad_position('div-gpt-ad-theengineerspost_com-box-4-0')}; It is the most common type of operation in all lathe machine operations. Save my name, email, and website in this browser for the next time I comment. Your style of writing the blog is excellent I am very impressed by your writing. This is something in between the parallel turning and facing off. What are Tactile Indicators, its Types and Uses? Holes are bored with the help of single point cutting tool. What is Geometric Dimensioning and Tolerancing? What is Capstan And Turret Lathe, and their Difference? When the tool is moved from right to the left we get the left-hand thread. The knurling tool is pressed against the job to perform the knurling operation. The lathe is run at high speeds from 1500 to 1800m per min, and oil is used on the emery cloth.if(typeof ez_ad_units!='undefined'){ez_ad_units.push([[300,250],'theengineerspost_com-leader-3','ezslot_9',677,'0','0'])};if(typeof __ez_fad_position!='undefined'){__ez_fad_position('div-gpt-ad-theengineerspost_com-leader-3-0')}; It is the process of reducing the diameter of a workpiece over a very narrow surface. Spring winding is the process of making a coiled spring by passing a wire around a mandrel which is revolved on a chuck or between centers. In external grooving, a tool moves radially into the side of the workpiece and removes the material along the cutting direction. It is that part of the lathe machine which is used to hold the workpiece. There are two types of grooving operations, external and face grooving. It is similar to shoulder work in external turning. Very basic things like knives, pens, and pencils are also tools. It is often performed after drilling to obtain both a more accurate diameter and a smoother internal finish. The factors should be used properly so that one can avoid from mishandling and mishaps while performing any kind of lathe operation. The amount of taper in the workpiece is usually specified on the basis of the difference in diameter of the taper to its length. He is also an author and editor at www.theengineerspost.com. Lathe Tool Bit HSS High-Speed Steel Square Lathe Tool Bit T42 10% Cobalt 3/8 x 3 (9.53 mm x 76.2 mm) IT Indian Tool Mfrs Pack Of 1 Piece Used for Turning, Boring. The factors should be used properly so that mishandling and mishaps are avoided in any type of lathe operation. The tailstock and carriage slide over the guideways. This operation is adopted in order to cut the metal parallel to the axis. How Precision Machining is Used in the Pharmaceutical Equipment? Some of the common lathe operations are: A lathe is a machine that rotates the workpiece about an axis of rotation to perform various operations such as turning, undercutting, knurling, drilling, facing, boring, and cutting, with lathe cutting tools that are applied to the workpiece to create an object with symmetry about that axis. A reamer enters the work piece axially through the end and it enlarges the existing hole to the diameter of the tool. Solar Power Plant Main Components, Working, Advantages and Disadvantages. (ii) Compound Rest:It is used to set the tool at a desired angle for taper turning and other operations. Lathe Operations Done By Using Special Attachments, Lathe Machine: Parts, Types, Accessories, Attachments, 7 Types Of Lathe Machine Chucks with [Images], Cutting speed, Feed, Depth of cut, Machining time in lathe machine, 14 Different Types of Lathe Cutting Tools, Drilling machine The complete guide Its Types, Operations and more [with pictures], http://engineering.myindialist.com/2009/working-principle-of-lathe-machine/, What is Jet Engines: Types of Jet Engines and Its Working, Grinding Machine: Types of Grinding Wheel And Grinding Machine Operation. Machine tools employ some sort of tool that does the cutting or shaping. In recent years, composites, such as carbon fiber, often used in the manufacture of aerospace components, have also become more popular. It can be used to shape pottery, the potters wheel is the latest well-known design made by a lathe. Chamfering on bolt helps to screw the nut easily. The process of removing material from hole of the workpiece is called boring. It is similar to the drilling process. It is done by a rotating tool, the rotating side of the cutter, known as a drilling drill. The surface finish is very good. There is a lot of operation used for using the lathe machine. This operation is done in case of bolt ends and shaft ends. The types of cutting tools well focus here is on milling and lathe cutting tools, including end mills, drills, and taps. Special purpose lathe. The general operations done with the lathe are grooving, turning, cutting, sanding and etc. It is done by a groove tool. The feeding is done by the carriage and the depth of cut is provided by the cross slide. whether we want to move the tool from left to right or right to left. The job held between the centre or a chuck and rotating at a required speed. The straight turning produces a cylindrical surface by removing excess metal from the workpiece. Enter your email address to subscribe to this blog and receive notifications of new posts by email. Tapper actually means making the work piece thinner or narrower towards one end.
(iii) Cross Slide:The cross slide is used to move the tool perpendicular to the axis of the lathe. The process of making threads on a cylindrical job is called threading. It also corrects out of the roundness of a hole. The tool is used called a counterbore. It is the main part of the lathe. Known as the mother of all machine tools, the lathe was the first machine tool that led to the invention of other machine tools. It is done using a knurling tool. They can perform other machining operations too. The pattern is usually a diamond shaped (criss-cross) pattern which is cut or rolled into the metal. In the turning operation, the tool generally reduces the diameter of the cylindrical workpiece, which can be done by cutting into the part for some depth and moving the tool parallel to the axis of the part. Internal tapers can be obtained accurately. With every cut desired the speed, depth, and feed of the lathe are changed for reasons of precision. In this operation, The workpiece is revolving in a chuck or a faceplate and the drill is held in the tailstock drill holder or drill chuck. The workpiece is rotating between the two centres i.e., live centre and dead centre os the lathe. While facing operation reduces the length of the piece, the tool is moved perpendicular to the axis of the part. It is done at the end of the hole, near the stepped shoulder of a cylindrical surface and at the end of a threaded portion in the blot. Engine lathe2. How Geothermal Power Plant Works Explained? For this operation, regular turning tool or facing tool may use. It is used to perform turning operations in which unwanted material is removed from a workpiece rotated against a cutting tool. The method is done at a faster rate.if(typeof ez_ad_units!='undefined'){ez_ad_units.push([[300,250],'theengineerspost_com-large-mobile-banner-1','ezslot_6',692,'0','0'])};if(typeof __ez_fad_position!='undefined'){__ez_fad_position('div-gpt-ad-theengineerspost_com-large-mobile-banner-1-0')}; The combined feed is made with the movement of a tool in longitudinal and lateral direction simultaneously while moving the workpiece. The general operations done with the lathe are grooving, turning, cutting, grinding, sanding, etc. As we discussed lathe has a wide range of applications in manufacturing industries. Several common products are produced with the help of lathe such as base ball bats, crankshafts,gun barrels, candle holders and much more. Metal working and wood turning are the common operations done in a lathe machine. What is a Slotting Machine and its Parts? In a lathe, the work is mounted on a chuck or on a faceplate and revolved at a very slow speed. Let's learn about these lathe machine more. Subscribe to newsletter to get latest updates through email. Knurling is a common manufacturing process typically done on a lathe, where a pattern of straight, angled or cross lines is rolled into the metal. Facing is a process where the work is rotated against a single point tool to make the end flat. Lathe can help to operate different machining operations such as knurling, drilling, turning etc. Metal spinning, thermal spraying, woodturning and metalworking are the common operations performed with a lathe machine. The workpiece is held on the chuck and it is made to rotate about the axis, and the tool is fed parallel to the lathe axis. Various operations are performed on a lathe machine.Each lathe operation has got its own factors that need to be considered before doing the work. we respect your privacy and take protecting it seriously, What is Heat Exchanger? The taper, which we are going to obtain, is equal to the resultant to the magnitude of the longitudinal and lateral feeds. A tap of the required size held on a special fixture is mounted on the tailstock spindle. Here three sets of centre holes are drilled. which are as follow. Unsourced material may be challenged and removed. The feed varies from 1 to 2 mm per revolution. To many grammatical errors but good content. If one is willing to change the angle then they can adjust the compound slide as they like. Plain or Straight Turning. It is done in order to remove the burrs, to protect the end of the workpiece from being damaged and to have a better look. A lathe is a large machine that rotates the work piece about its axis of rotation and cutting is done using a non rotating singular cutting tool. A wide variety of materials can be cut on a lathe from metals, such as brass, stainless steel and copper, through to more complex materials, including superalloys, such as Inconel. This operation of reducing a flat surface on the end of the workpiece. It is then rotated about its axis and then the cutting process starts. In the lathe machine, we generally use three-jaw or four-jaw check. It is process in which a convex, concave or any irregular surface is formed on the workpiece with the help of a forming tool. Notify me of follow-up comments by email. Undercutting is done at the end of an internal thread or a counterbore to provide clearance for the tool or any part. The straight type is used for wider surface and the circular type for narrow surfaces. It is a turning operation in which turning is performed at a different axis on a single setting of a job. Boring is the operation of enlarging the hole which is already drilled, punched or forged. All the parts of the lathe are bolted on the bed. The reamer is held on the tailstock spindle, either directly or through a drill chuck, and is held stationary while the work is revolved at a very slow speed. ins.dataset.adChannel=cid;if(ffid==2){ins.dataset.fullWidthResponsive='true';} The chips fell into the bed of the lathe. Lets discuss all lathe machine operations one by one as follows.if(typeof ez_ad_units!='undefined'){ez_ad_units.push([[580,400],'theengineerspost_com-medrectangle-3','ezslot_2',683,'0','0'])};if(typeof __ez_fad_position!='undefined'){__ez_fad_position('div-gpt-ad-theengineerspost_com-medrectangle-3-0')}; To perform different lathe machine operations on a lathe, the workpiece may be supported and driven by any one of the following methods: The above methods of holding the work may be classified under two heading: The lathe machine operations are classified into three main categories and are as follows. Required fields are marked *. Ornamental lathes can produce three-dimensional solids of incredible complexity. Operations Done by Holding Workpiece Between Centres, 2. Special tools are used in order to perform these various operations. Cutting tool materials must be harder than the material of the workpiece, even at high temperatures during the process. Such cutters are also often referred to by the set-phrase name of single-point cutting tool, as distinguished from other cutting tools such as a saw or water jet cutter. With every cut desired the speed, depth and feed of the lathe machine is changed for precision. Workpiece held by a chuck or any other fixtures. This pattern helps human hands or fingers to get a better grip on the knurled object than finish provided by the originally-smooth metal surface. To provide an accurate surface from which to take measurements. For internal grinding, the work must be revolved on a chuck or faceplate. (i) Tool Post:It is used to hold the tool. How Many Galaxies are there in the Universe?
These are the various operations performed on a lathe machine. Drilling operation is the process of making an initial hole in a work piece. Metric taper is available in seven standard sizes with standard taper angles. Knurling is done at the lowest speed available on a lathe. This operation is performed by feeding the tool perpendicular to the axis of rotation of the chuck. The depth of cut is given by vertical adjustment of the work provided by the attachment. if anyone wants to operate the lathe machine then he must first know about the feeds, cutting speed, depth of the cut and usage of tool should be considered.
A lathe is a machine that rotates the piece on the axis in order to perform various operations like cutting, facing, knurling, deformation, and more. What is Milling Machine Operation, Parts and Types. Undercutting is similar to a grooving operation when performed inside a hole. A lathe is a machining tool that is used primarily for shaping metal or wood. Turning Operation. Examples of various objects that are produced by lathe are candlestick holders, gun barrels, cue sticks, table legs, bowls, baseball bats, musical instruments, crankshafts, and camshafts. In parting operation the tool is moved in or out of the work piece. In this article, you will learn about what are the different types of lathe machine operations performed on the lathe machine. Lathe chuck supports the work piece. Guideways are present on the bed. It is aligned with the tailstock. The taper angle is the angle at which the compound rest to be rotated is calculated by using the formula tan = D-d / 21, where, D= bigger diameter, d = smaller diameter, l = length of the workpiece. In turning operation, the excess material is removed from the surface of the workpiece to produce a cylindrical surface of desired shape and size. Boring is similar to the external turning operation and can be performed in a lathe. It is basically used to reduce the diameter of the work piece. The feeding tool is at an angle to the axis of rotation of the workpiece.if(typeof ez_ad_units!='undefined'){ez_ad_units.push([[250,250],'theengineerspost_com-mobile-leaderboard-1','ezslot_13',679,'0','0'])};if(typeof __ez_fad_position!='undefined'){__ez_fad_position('div-gpt-ad-theengineerspost_com-mobile-leaderboard-1-0')}; A boring tool is mounted on the tool post and by swivelling the compound slide to the desired angle, a short taper hole is machined by hand feeding.
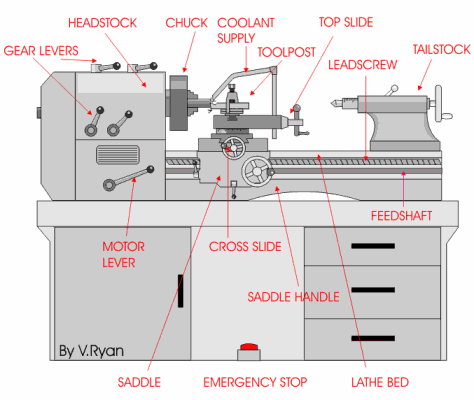
The working of the lathe machine changes with every operation and cut desired. A lathe is a machine that rotates the piece on the axis in order to perform various operations like cutting, facing, knurling, deformation and more. A tool bit is a non-rotary cutting tool used in metal lathes, shapers, and planers. Here the taper length obtain is equal to the width of the form tool. Your email address will not be published. This method is adopted for the drilling of regular-shaped workpiece. large size tapers can be easily obtained. Lathe machine are of different types according the types of work performed. This is done to provide a better gripping surface when operated by hands.
Some of the common lathe operations are: This is usually the first step of any lathe operation on the lathe machine. The working of the lathe machine changes with every operation and cut desired. Chamfering is the process of beveling the extreme ends of a workpiece. It consists of a boring bar having a single-point cutting tool that enlarges the hole. There are several lathe cutting tools that help in cutting with the lathe machine. 10. Some common lathe operations are drilling, knurling, turning, facing, grooving, parting, threading, boring, and tapping. It is present at the right-hand side of the lathe. A grooving tool is similar to the parting-off tool. During taper turning the feed is set at an angle to the workpiece. The tool is used is called the reamer, which has multi-plate cutting edges. Chamfering is used in woodworking,glass cutting,architecture, and in CAD, and its also a useful tool for deburring. Keep visiting. For to make the cut deeper the parting tool is pulled out and transferred to the side for the cut and to prevent the tool from breaking. In face grooving, the tool machines groove in the face of the workpiece.
Eccentric Turning. The most commonly used lathes are the woodworking lathes. For the grinding external surface, the work may be revolved between centres or on a chuck. That is it, thanks for reading. These factors should be used carefully so that one can avoid from mishandling and mishaps while performing any kind of lathe operation on a lathe machine. Support is also given from the tailstock end. To obtain the required size of the taper the form tool is fed slowly straight into the workpiece by operating the cross slide perpendicular to the lathe axis. It is made of cast iron. When the threads or helical grooves are formed on the out surface of the workpiece is called external thread cutting. The drill is held in the tailstock and the drilling operation is done by advancing the drill in the workpiece by rotating the handle of the tailstock. Some examples of tools that are often used today are the hammer, the wrench (also called a spanner), saws, shovel, telephone, and the computer. The taper angle is calculated similarly to the. This method is useful for small tapers. This includes speed lathe, engine lathe, tool-room lathe, special-purpose lathe, CNC lathe etc. Compound rest can be swivelled to the required angle .
It is a machining operation that is done to produce flat surfaces at the ends of the workpiece. Nuclear Power Plant Working Principle, Advantages, Disadvantages with Diagram. Great article for lathe machineThanks for sharing this resource article on lathe machine tools. Metal spinning, thermal spraying, woodturning, and metalworking are the common operations performed with a lathe machine. Each lathe operation has its own factors that must be considered before starting work. Chip pan is used to collect the chips that are produced during the lathe operation. It comprises of headstock, tailstock, carriage guideways and other parts. Shoulder Turning. The lathe machine operations are given below : 7 Main differences between brazing and soldering (Simplified), 6 Important Types of Manufacturing Processes [2021]. Lathe machine operations are performed by using special attachments: Milling is the operation of removing metal by feeding the work against a rotating cutter having multiple cutting edges.var asau='8288738383';var cid='8918976548';var pid='ca-pub-9958205674121742';var slotId='div-gpt-ad-theengineerspost_com-leader-4-0';var ffid=1;var alS=1710%1000;var container=document.getElementById(slotId);container.style.width='100%';var ins=document.createElement('ins');ins.id=slotId+'-asloaded';ins.className='adsbygoogle ezasloaded';ins.dataset.adClient=pid;if(typeof window.adsenseNoUnit=='undefined'){ins.dataset.adSlot=asau;} A lathe is a machine tool which is used to rotate a workpiece to perform various operations such as turning, facing, knurling, grooving etc., with the help of tools that are applied to the workpiece. And much more can be done with lathe machine. A taper is the uniform increase or decrease in the diameter of the workpiece and measured along with its length. 2022 The Engineers Post - All Rights Reserved / Contact-, 22 Types of Lathe Machine Operations [Complete Guide], 1. The three jaw of the three jaw chuck is made to move simultaneously but the jaws of the four jaw chuck moves independently. Following are the Lathe machine operations done either by holding the workpiece between centres or by a chuck: Lathe machine operations which are performed by holding the work by a chuck or a faceplate or an angle plate are: The operation which is performed by using special attachments are: Read Also about Lathe Machine:if(typeof ez_ad_units!='undefined'){ez_ad_units.push([[336,280],'theengineerspost_com-box-4','ezslot_4',672,'0','0'])};if(typeof __ez_fad_position!='undefined'){__ez_fad_position('div-gpt-ad-theengineerspost_com-box-4-0')}; It is the most common type of operation in all lathe machine operations. Save my name, email, and website in this browser for the next time I comment. Your style of writing the blog is excellent I am very impressed by your writing. This is something in between the parallel turning and facing off. What are Tactile Indicators, its Types and Uses? Holes are bored with the help of single point cutting tool. What is Geometric Dimensioning and Tolerancing? What is Capstan And Turret Lathe, and their Difference? When the tool is moved from right to the left we get the left-hand thread. The knurling tool is pressed against the job to perform the knurling operation. The lathe is run at high speeds from 1500 to 1800m per min, and oil is used on the emery cloth.if(typeof ez_ad_units!='undefined'){ez_ad_units.push([[300,250],'theengineerspost_com-leader-3','ezslot_9',677,'0','0'])};if(typeof __ez_fad_position!='undefined'){__ez_fad_position('div-gpt-ad-theengineerspost_com-leader-3-0')}; It is the process of reducing the diameter of a workpiece over a very narrow surface. Spring winding is the process of making a coiled spring by passing a wire around a mandrel which is revolved on a chuck or between centers. In external grooving, a tool moves radially into the side of the workpiece and removes the material along the cutting direction. It is that part of the lathe machine which is used to hold the workpiece. There are two types of grooving operations, external and face grooving. It is similar to shoulder work in external turning. Very basic things like knives, pens, and pencils are also tools. It is often performed after drilling to obtain both a more accurate diameter and a smoother internal finish. The factors should be used properly so that one can avoid from mishandling and mishaps while performing any kind of lathe operation. The amount of taper in the workpiece is usually specified on the basis of the difference in diameter of the taper to its length. He is also an author and editor at www.theengineerspost.com. Lathe Tool Bit HSS High-Speed Steel Square Lathe Tool Bit T42 10% Cobalt 3/8 x 3 (9.53 mm x 76.2 mm) IT Indian Tool Mfrs Pack Of 1 Piece Used for Turning, Boring. The factors should be used properly so that mishandling and mishaps are avoided in any type of lathe operation. The tailstock and carriage slide over the guideways. This operation is adopted in order to cut the metal parallel to the axis. How Precision Machining is Used in the Pharmaceutical Equipment? Some of the common lathe operations are: A lathe is a machine that rotates the workpiece about an axis of rotation to perform various operations such as turning, undercutting, knurling, drilling, facing, boring, and cutting, with lathe cutting tools that are applied to the workpiece to create an object with symmetry about that axis. A reamer enters the work piece axially through the end and it enlarges the existing hole to the diameter of the tool. Solar Power Plant Main Components, Working, Advantages and Disadvantages. (ii) Compound Rest:It is used to set the tool at a desired angle for taper turning and other operations. Lathe Operations Done By Using Special Attachments, Lathe Machine: Parts, Types, Accessories, Attachments, 7 Types Of Lathe Machine Chucks with [Images], Cutting speed, Feed, Depth of cut, Machining time in lathe machine, 14 Different Types of Lathe Cutting Tools, Drilling machine The complete guide Its Types, Operations and more [with pictures], http://engineering.myindialist.com/2009/working-principle-of-lathe-machine/, What is Jet Engines: Types of Jet Engines and Its Working, Grinding Machine: Types of Grinding Wheel And Grinding Machine Operation. Machine tools employ some sort of tool that does the cutting or shaping. In recent years, composites, such as carbon fiber, often used in the manufacture of aerospace components, have also become more popular. It can be used to shape pottery, the potters wheel is the latest well-known design made by a lathe. Chamfering on bolt helps to screw the nut easily. The process of removing material from hole of the workpiece is called boring. It is similar to the drilling process. It is done by a rotating tool, the rotating side of the cutter, known as a drilling drill. The surface finish is very good. There is a lot of operation used for using the lathe machine. This operation is done in case of bolt ends and shaft ends. The types of cutting tools well focus here is on milling and lathe cutting tools, including end mills, drills, and taps. Special purpose lathe. The general operations done with the lathe are grooving, turning, cutting, sanding and etc. It is done by a groove tool. The feeding is done by the carriage and the depth of cut is provided by the cross slide. whether we want to move the tool from left to right or right to left. The job held between the centre or a chuck and rotating at a required speed. The straight turning produces a cylindrical surface by removing excess metal from the workpiece. Enter your email address to subscribe to this blog and receive notifications of new posts by email. Tapper actually means making the work piece thinner or narrower towards one end.
(iii) Cross Slide:The cross slide is used to move the tool perpendicular to the axis of the lathe. The process of making threads on a cylindrical job is called threading. It also corrects out of the roundness of a hole. The tool is used called a counterbore. It is the main part of the lathe. Known as the mother of all machine tools, the lathe was the first machine tool that led to the invention of other machine tools. It is done using a knurling tool. They can perform other machining operations too. The pattern is usually a diamond shaped (criss-cross) pattern which is cut or rolled into the metal. In the turning operation, the tool generally reduces the diameter of the cylindrical workpiece, which can be done by cutting into the part for some depth and moving the tool parallel to the axis of the part. Internal tapers can be obtained accurately. With every cut desired the speed, depth, and feed of the lathe are changed for reasons of precision. In this operation, The workpiece is revolving in a chuck or a faceplate and the drill is held in the tailstock drill holder or drill chuck. The workpiece is rotating between the two centres i.e., live centre and dead centre os the lathe. While facing operation reduces the length of the piece, the tool is moved perpendicular to the axis of the part. It is done at the end of the hole, near the stepped shoulder of a cylindrical surface and at the end of a threaded portion in the blot. Engine lathe2. How Geothermal Power Plant Works Explained? For this operation, regular turning tool or facing tool may use. It is used to perform turning operations in which unwanted material is removed from a workpiece rotated against a cutting tool. The method is done at a faster rate.if(typeof ez_ad_units!='undefined'){ez_ad_units.push([[300,250],'theengineerspost_com-large-mobile-banner-1','ezslot_6',692,'0','0'])};if(typeof __ez_fad_position!='undefined'){__ez_fad_position('div-gpt-ad-theengineerspost_com-large-mobile-banner-1-0')}; The combined feed is made with the movement of a tool in longitudinal and lateral direction simultaneously while moving the workpiece. The general operations done with the lathe are grooving, turning, cutting, grinding, sanding, etc. As we discussed lathe has a wide range of applications in manufacturing industries. Several common products are produced with the help of lathe such as base ball bats, crankshafts,gun barrels, candle holders and much more. Metal working and wood turning are the common operations done in a lathe machine. What is a Slotting Machine and its Parts? In a lathe, the work is mounted on a chuck or on a faceplate and revolved at a very slow speed. Let's learn about these lathe machine more. Subscribe to newsletter to get latest updates through email. Knurling is a common manufacturing process typically done on a lathe, where a pattern of straight, angled or cross lines is rolled into the metal. Facing is a process where the work is rotated against a single point tool to make the end flat. Lathe can help to operate different machining operations such as knurling, drilling, turning etc. Metal spinning, thermal spraying, woodturning and metalworking are the common operations performed with a lathe machine. The workpiece is held on the chuck and it is made to rotate about the axis, and the tool is fed parallel to the lathe axis. Various operations are performed on a lathe machine.Each lathe operation has got its own factors that need to be considered before doing the work. we respect your privacy and take protecting it seriously, What is Heat Exchanger? The taper, which we are going to obtain, is equal to the resultant to the magnitude of the longitudinal and lateral feeds. A tap of the required size held on a special fixture is mounted on the tailstock spindle. Here three sets of centre holes are drilled. which are as follow. Unsourced material may be challenged and removed. The feed varies from 1 to 2 mm per revolution. To many grammatical errors but good content. If one is willing to change the angle then they can adjust the compound slide as they like. Plain or Straight Turning. It is done in order to remove the burrs, to protect the end of the workpiece from being damaged and to have a better look. A lathe is a large machine that rotates the work piece about its axis of rotation and cutting is done using a non rotating singular cutting tool. A wide variety of materials can be cut on a lathe from metals, such as brass, stainless steel and copper, through to more complex materials, including superalloys, such as Inconel. This operation of reducing a flat surface on the end of the workpiece. It is then rotated about its axis and then the cutting process starts. In the lathe machine, we generally use three-jaw or four-jaw check. It is process in which a convex, concave or any irregular surface is formed on the workpiece with the help of a forming tool. Notify me of follow-up comments by email. Undercutting is done at the end of an internal thread or a counterbore to provide clearance for the tool or any part. The straight type is used for wider surface and the circular type for narrow surfaces. It is a turning operation in which turning is performed at a different axis on a single setting of a job. Boring is the operation of enlarging the hole which is already drilled, punched or forged. All the parts of the lathe are bolted on the bed. The reamer is held on the tailstock spindle, either directly or through a drill chuck, and is held stationary while the work is revolved at a very slow speed. ins.dataset.adChannel=cid;if(ffid==2){ins.dataset.fullWidthResponsive='true';} The chips fell into the bed of the lathe. Lets discuss all lathe machine operations one by one as follows.if(typeof ez_ad_units!='undefined'){ez_ad_units.push([[580,400],'theengineerspost_com-medrectangle-3','ezslot_2',683,'0','0'])};if(typeof __ez_fad_position!='undefined'){__ez_fad_position('div-gpt-ad-theengineerspost_com-medrectangle-3-0')}; To perform different lathe machine operations on a lathe, the workpiece may be supported and driven by any one of the following methods: The above methods of holding the work may be classified under two heading: The lathe machine operations are classified into three main categories and are as follows. Required fields are marked *. Ornamental lathes can produce three-dimensional solids of incredible complexity. Operations Done by Holding Workpiece Between Centres, 2. Special tools are used in order to perform these various operations. Cutting tool materials must be harder than the material of the workpiece, even at high temperatures during the process. Such cutters are also often referred to by the set-phrase name of single-point cutting tool, as distinguished from other cutting tools such as a saw or water jet cutter. With every cut desired the speed, depth and feed of the lathe machine is changed for precision. Workpiece held by a chuck or any other fixtures. This pattern helps human hands or fingers to get a better grip on the knurled object than finish provided by the originally-smooth metal surface. To provide an accurate surface from which to take measurements. For internal grinding, the work must be revolved on a chuck or faceplate. (i) Tool Post:It is used to hold the tool. How Many Galaxies are there in the Universe?
These are the various operations performed on a lathe machine. Drilling operation is the process of making an initial hole in a work piece. Metric taper is available in seven standard sizes with standard taper angles. Knurling is done at the lowest speed available on a lathe. This operation is performed by feeding the tool perpendicular to the axis of rotation of the chuck. The depth of cut is given by vertical adjustment of the work provided by the attachment. if anyone wants to operate the lathe machine then he must first know about the feeds, cutting speed, depth of the cut and usage of tool should be considered.
A lathe is a machine that rotates the piece on the axis in order to perform various operations like cutting, facing, knurling, deformation, and more. What is Milling Machine Operation, Parts and Types. Undercutting is similar to a grooving operation when performed inside a hole. A lathe is a machining tool that is used primarily for shaping metal or wood. Turning Operation. Examples of various objects that are produced by lathe are candlestick holders, gun barrels, cue sticks, table legs, bowls, baseball bats, musical instruments, crankshafts, and camshafts. In parting operation the tool is moved in or out of the work piece. In this article, you will learn about what are the different types of lathe machine operations performed on the lathe machine. Lathe chuck supports the work piece. Guideways are present on the bed. It is aligned with the tailstock. The taper angle is the angle at which the compound rest to be rotated is calculated by using the formula tan = D-d / 21, where, D= bigger diameter, d = smaller diameter, l = length of the workpiece. In turning operation, the excess material is removed from the surface of the workpiece to produce a cylindrical surface of desired shape and size. Boring is similar to the external turning operation and can be performed in a lathe. It is basically used to reduce the diameter of the work piece. The feeding tool is at an angle to the axis of rotation of the workpiece.if(typeof ez_ad_units!='undefined'){ez_ad_units.push([[250,250],'theengineerspost_com-mobile-leaderboard-1','ezslot_13',679,'0','0'])};if(typeof __ez_fad_position!='undefined'){__ez_fad_position('div-gpt-ad-theengineerspost_com-mobile-leaderboard-1-0')}; A boring tool is mounted on the tool post and by swivelling the compound slide to the desired angle, a short taper hole is machined by hand feeding.