The collector or discharge pipe may also contain valves and instrumentation to control the compressor. Hybrid versions of vaned diffusers include wedge (see Figure 1.3), channel, and pipe diffusers. Thank you for your submission. A simple centrifugal compressor stage has four components (listed in order of throughflow): inlet, impeller/rotor, diffuser, and collector. [10][39] Until recently, limitations in computational power, forced these equations to be simplified to an Inviscid two-dimensional problem with pseudo losses. In summary; most industrial and commercial centrifugal compressors are selected or designed to operate at or near their highest efficiencies and to avoid operation at low efficiencies. This assumption is not acceptable in practice as inlet temperature variations cause significant variations in compressor performance. {\displaystyle \gamma =C_{p}/C_{v}}
They may include other components such as an inlet throttle valve, a shrouded port, an annular duct (see Figure 1.1), a bifurcated duct, stationary guide vanes/airfoils used to straight or swirl flow (see Figure 1.1), movable guide vanes (used to vary pre-swirl adjustably). {\displaystyle T} Under specific conditions, the operation of a Centrifugal compressor is considered a reversible process. Generally accepted nomenclature might refer to the diffuser's lead edge as station 3 and the trailing edge as station 4. We are an equal opportunity employer and are dedicated to hiring qualified protected veterans and individuals with disabilities. This location may occur at the impeller inlet "throat" or at the vaned diffuser inlet "throat". Impellers are designed in many configurations including "open" (visible blades), "covered or shrouded", "with splitters" (every other inducer removed), and "w/o splitters" (all full blades). Typically for high speed equipment, as flow increases the velocity of the flow can approach sonic speed somewhere within the compressor stage. The horizontal axis represents the energy equation derivable from The first law of thermodynamics.
Your personalized homepage experience is available here. Particularly, performance parameters such as efficiencies and loss-coefficients, which are also dimensionless. Centrifugal compressors also look very similar to their turbomachinery counterpart the radial turbine as shown in the figure.
Diffusers can be vaneless, vaned, or an alternating combination.
m [4] In contrast, fans or blowers are often considered to have density increases of less than five percent and peak relative fluid velocities below Mach 0.3. Only see the articles on the blog you are interested in reading.
Compared to estimating performance which is very cost effective (thus useful in design), testing, while costly, is still the most precise method.
Amano, The Development of a Centrifugal Compressor Impeller, International Journal for Computational Methods in Engineering Science and Mechanics, Volume 10 Issue 4 2009, Pages 290 301. Our MSG TURBO-AIR solutions are designed for operations with limited or no supply of water available for cooling, as instead, it contains multiple air-cooled heat exchangers for its lubrication system and the different stages of discharged air. = Bernoulli's fluid dynamic principle plays an important role in understanding vaneless stationary components like an inlet. Compared to other machines of a comparable capacity, this solution can operate at its highest level of efficiency at full load, part load and no-load leaving you with little time to fall behind your competitors. A diagonal stage is used in the Pratt & Whitney Canada PW600 series of small turbofans. You may personalize your experience at any time during your visit. Choke occurs under one of 2 conditions. [1][14] Key contributors of technical achievements that pushed the practical application of turbomachinery forward include:[15][16] Denis Papin,[17] Kernelien Le Demour, Daniel Gabriel Fahrenheit, John Smeaton, Dr. A. C. E. Rateau,[18] John Barber, Alexander Sablukov, Sir Charles Algernon Parsons, gidius Elling, Sanford Alexander Moss, Willis Carrier, Adolf Busemann, Hermann Schlichting, Frank Whittle and Hans von Ohain. Alternately, in wastewater treatment plants, low pressure, single-stage applications are used to achieve the desired pressure ratio. It may be found interesting that the specific speed coefficient may be used in place of speed to define the y-axis of Figure 1.2, while at the same time, the specific diameter coefficient may be in place of diameter to define the z-axis. T
Unlike displacement compressors that work at a constant flow, dynamic compressors work at a constant pressure and the performance is affected by external conditions such as changes in inlet temperatures. Most of the hydrocarbon gases such as methane and ethylene are best modeled as a real gas equation of state rather than ideal gases. Ingersoll Rand Rental Agreement Terms & Conditions, Trust Ingersoll Rand to deliver the most effective air quality and treatment solutions, Centrifugal compressors incorporating the latest technology that can be used over a wide range of industries, Reliable, durable, low maintenance compressors.
Modern industrial compressors are often needed to achieve specific performance goals across a range of flows and pressures; thus taking a significant step toward the sophistication seen in gas turbine applications. Figure 2.2 (shown right) represents the physical or mechanical domain of turbomachinery.
= The key difference between such compressors and pumps is that the compressor working fluid is a gas (compressible) and the pump working fluid is liquid (incompressible). The shape of Figure 5.2's speed-lines provides a good example of why it is inappropriate to use the term choke in association with a maximum flow of all centrifugal compressor speed-lines. This turboshaft (or turboprop) impeller is rotating counter-clockwise when looking downstream into the compressor. Professional societies such as ASME (i.e. For example, a variation of the first parameter shown below is popularly used in aircraft engine system analysis.
Ingersoll Rand represents brands that have stood the test of time.
[35] It is standard in these cases that the equivalent temperature, equivalent pressure, and gas is specified explicitly or implied at a standard condition. PTC10, Fluid Meters Handbook, PTC-19.x),[34] ASHRAE (ASHRAE Handbook) and API (ANSI/API 6172002, 6722007)[31][33] have established standards for detailed experimental methods and analysis of test results. Your personalized homepage experience is available here. This is because it is nearly impossible to change one of these parameters independently. Bernoulli's fluid dynamic principle is of great value in understanding this problem. {\displaystyle \delta Q=TdS} [12] In contrast, all volume flow specifications require the additional specification of density. is the specific heat at constant volume, and The stationary compressor is ducting with increasing flow-area where energy transformation takes place. The inclusion of efficiency islands effectively generates a 3-dimensional topology to this 2-dimensional map. Most modern high-efficiency impellers use "backsweep" in the blade shape.[2][3][4]. The Wikipedia entry for equations of state is very thorough. The fifth parameter, specific diameter, is a less often discussed dimensionless parameter found useful by Balje.[38].
another impeller or a combustor, flow losses can be reduced by directing the flow with stationary turning vanes or individual turning pipes (pipe diffusers). The above equation is known as the fundamental thermodynamic relation. They provide for the creation of additional relationships (being dimensionless) found valuable in the characterization of performance. S These innovative additions have so far been embraced by our customers as the future of centrifugal compressors by offering a more time and energy-efficient solution to all of your industrial needs. The benefit of an oil-less solution is that it also prevents any contamination within the system and limits the risk of any compressed air pipeline fires caused by oil carryover. This of course would mean the two turbomachines being compared are similar, both geometrically and in terms of performance. At Ingersoll Rand, we have expanded our portfolio of centrifugal air compressor solutions to incorporate the latest technology into our range. is entropy. They all fit one of two categories: The pressure rise may alternatively be specified as a ratio that has no units: Other features common to performance maps are: The two most common methods for producing a map for a centrifugal compressor are at constant shaft speed or with a constant throttle setting. Higher pressure ratio turbocharger centrifugal compressors exhibit this same phenomenon. With regard to the equation of state, it is important to remember that while air and nitrogen properties (near standard atmospheric conditions) are easily and accurately estimated by this simple relationship, there are many centrifugal compressor applications where the ideal relationship is inadequate. The two plots show that the pressure rises between the compressor inlet (station 1) and compressor exit (station 2).
As a company, we ensure superior components and quality with no exception and are globally backed due to our years of expertise and knowledge.
Air is drawn into the center of a rotating impeller with radial blades and is pushed toward the center by centrifugal force. Assuming dry air, and the ideal gas equation of state and an isentropic process, there is enough information to define the pressure ratio and efficiency for this one point. A derivation of the general Euler equations (fluid dynamics) is Euler's pump and turbine equation, which plays an important role in understanding impeller performance. [14] Mathematicians and physicists who established the foundations of this aero-thermo domain include:[15][16] Isaac Newton, Daniel Bernoulli, Leonhard Euler, Claude-Louis Navier, George Stokes, Ernst Mach, Nikolay Yegorovich Zhukovsky, Martin Kutta, Ludwig Prandtl, Theodore von Krmn, Paul Richard Heinrich Blasius, and Henri Coand.
Pressure ratio and flow are the main parameters[15][31][33][34] needed to match the Figure 5.2 performance map to a simple compressor application. In many cases, the flow leaving the centrifugal impeller is traveling near the speed of sound.
This creates a practical problem when trying to experimentally determine the effect of any one parameter. Over the past 100 years, applied scientists including Stodola (1903, 19271945),[7] Pfleiderer (1952),[8] Hawthorne (1964),[9] Shepherd (1956),[1] Lakshminarayana (1996),[10] and Japikse (many texts including citations),[2][11][citation needed][12] have educated young engineers in the fundamentals of turbomachinery. While illustrating a gas turbine's Brayton cycle,[15] Figure 5.1 includes example plots of pressure-specific volume and temperature-entropy. Centrifugal compressors are used throughout industry because they have fewer rubbing parts, are relatively energy efficient, and give higher and non-, Centrifugal compressors are mostly used as, Their main drawback is that they cannot achieve the high, Centrifugal compressors are impractical, compared to axial compressors, for use in large, This page was last edited on 6 July 2022, at 00:41. As described in Bernoulli's principle, the reduction in velocity causes the pressure to rise.[1]. Turbomachinery analysts gain tremendous insight into performance by comparisons of the 5 parameters shown in the above table. In general application, the Flow-coefficient and Head-coefficient are considered of primary importance. Choose a different country or region to see the content specific to your location. In most cases the reason for this is that close to Mach 1 velocities have been reached somewhere within the impeller and/or diffuser generating a rapid increase in losses. [1][14] Within the physical domain the vertical axis differentiates between high speeds and low speeds depending upon the turbomachinery application. C [37] This stalling flow reversal may go unnoticed as the fraction of mass flow or energy is too low. Both are shown in the adjacent photograph of an engine with 5 stages of axial compressors and one stage of a centrifugal compressor. Depending on the pressure required for the application, a number of stages can be arranged in a series to achieve a higher pressure. = is the specific heat at constant pressure.
In the case where flow passes through a straight pipe to enter a centrifugal compressor, the flow is axial, uniform, and has no vorticity, i.e. This is due to requiring fewer stages to achieve the same pressure rise. In many industrial applications, it may be necessary to increase the stall line due to the system backpressure. The reversed flow exiting the impeller inlet exhibits a strong rotational component, which affects lower radius flow angles (closer to the impeller hub) at the leading edge of the blades. Lines of constant power could just as easily be substituted. Personalize your experience on the Compressed Air Blog.
For this reason, it is only necessary to summarize that in the ideal case, the lowest specific fuel consumption would occur when the centrifugal compressor's peak efficiency curve coincides with the gas turbine's required operation line. The simplest inlet to a centrifugal compressor is typically a simple pipe. {\displaystyle C_{p}} Another example are centrifugal compressors design and built for the petroleum industry. Also termed continuity, this fundamental equation written in general form is as follows: Also termed the NavierStokes equations, this fundamental is derivable from Newton's second law when applied to fluid motion. Upon inspection it may be noticed that each of these points has been taken near 56% efficiency. Bernoulli's fluid dynamic principle plays an important role in understanding diffuser performance. where However, if the machine is forced to surge repeatedly for a long period of time, or if it is poorly designed, repeated surges can result in a catastrophic failure. When the diffuser discharges into a large empty circumferentially (constant area) chamber, the collector may be termed a Plenum.
Personalize your experience by selecting the topics you are interested in below. Generally, the accepted mathematical nomenclature refers to the leading edge of the impeller with subscript 1. You may edit your selections at any time. The first three speed-lines have 6 points each while the highest speed line has five. Depending upon its use/application inlets can be very complex. Figure 5.2, a centrifugal compressor performance map (either test or estimated), shows the flow, pressure ratio for each of 4 speed-lines (total of 23 data points). swirling motion. Built up by more than 160 years of acquisitions and innovations, today's Ingersoll Rand brands offer market-leading solutions and services to help make life better. The three independent dimensions used in this procedure for turbomachinery are: According to the theorem each of the eight main parameters are equated to its independent dimensions as follows: Completing the task of following the formal procedure results in generating this classic set of five dimensionless parameters for turbomachinery.
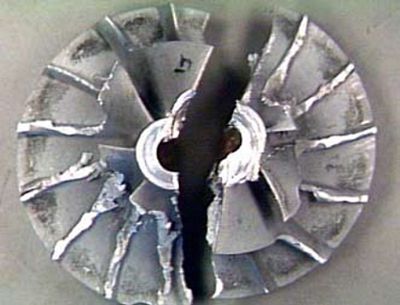
Your personalized homepage experience is available here. Particularly, performance parameters such as efficiencies and loss-coefficients, which are also dimensionless. Centrifugal compressors also look very similar to their turbomachinery counterpart the radial turbine as shown in the figure.

m [4] In contrast, fans or blowers are often considered to have density increases of less than five percent and peak relative fluid velocities below Mach 0.3. Only see the articles on the blog you are interested in reading.
Compared to estimating performance which is very cost effective (thus useful in design), testing, while costly, is still the most precise method.
Amano, The Development of a Centrifugal Compressor Impeller, International Journal for Computational Methods in Engineering Science and Mechanics, Volume 10 Issue 4 2009, Pages 290 301. Our MSG TURBO-AIR solutions are designed for operations with limited or no supply of water available for cooling, as instead, it contains multiple air-cooled heat exchangers for its lubrication system and the different stages of discharged air. = Bernoulli's fluid dynamic principle plays an important role in understanding vaneless stationary components like an inlet. Compared to other machines of a comparable capacity, this solution can operate at its highest level of efficiency at full load, part load and no-load leaving you with little time to fall behind your competitors. A diagonal stage is used in the Pratt & Whitney Canada PW600 series of small turbofans. You may personalize your experience at any time during your visit. Choke occurs under one of 2 conditions. [1][14] Key contributors of technical achievements that pushed the practical application of turbomachinery forward include:[15][16] Denis Papin,[17] Kernelien Le Demour, Daniel Gabriel Fahrenheit, John Smeaton, Dr. A. C. E. Rateau,[18] John Barber, Alexander Sablukov, Sir Charles Algernon Parsons, gidius Elling, Sanford Alexander Moss, Willis Carrier, Adolf Busemann, Hermann Schlichting, Frank Whittle and Hans von Ohain. Alternately, in wastewater treatment plants, low pressure, single-stage applications are used to achieve the desired pressure ratio. It may be found interesting that the specific speed coefficient may be used in place of speed to define the y-axis of Figure 1.2, while at the same time, the specific diameter coefficient may be in place of diameter to define the z-axis. T
Unlike displacement compressors that work at a constant flow, dynamic compressors work at a constant pressure and the performance is affected by external conditions such as changes in inlet temperatures. Most of the hydrocarbon gases such as methane and ethylene are best modeled as a real gas equation of state rather than ideal gases. Ingersoll Rand Rental Agreement Terms & Conditions, Trust Ingersoll Rand to deliver the most effective air quality and treatment solutions, Centrifugal compressors incorporating the latest technology that can be used over a wide range of industries, Reliable, durable, low maintenance compressors.

Modern industrial compressors are often needed to achieve specific performance goals across a range of flows and pressures; thus taking a significant step toward the sophistication seen in gas turbine applications. Figure 2.2 (shown right) represents the physical or mechanical domain of turbomachinery.
= The key difference between such compressors and pumps is that the compressor working fluid is a gas (compressible) and the pump working fluid is liquid (incompressible). The shape of Figure 5.2's speed-lines provides a good example of why it is inappropriate to use the term choke in association with a maximum flow of all centrifugal compressor speed-lines. This turboshaft (or turboprop) impeller is rotating counter-clockwise when looking downstream into the compressor. Professional societies such as ASME (i.e. For example, a variation of the first parameter shown below is popularly used in aircraft engine system analysis.
Ingersoll Rand represents brands that have stood the test of time.
[35] It is standard in these cases that the equivalent temperature, equivalent pressure, and gas is specified explicitly or implied at a standard condition. PTC10, Fluid Meters Handbook, PTC-19.x),[34] ASHRAE (ASHRAE Handbook) and API (ANSI/API 6172002, 6722007)[31][33] have established standards for detailed experimental methods and analysis of test results. Your personalized homepage experience is available here. This is because it is nearly impossible to change one of these parameters independently. Bernoulli's fluid dynamic principle is of great value in understanding this problem. {\displaystyle \delta Q=TdS} [12] In contrast, all volume flow specifications require the additional specification of density. is the specific heat at constant volume, and The stationary compressor is ducting with increasing flow-area where energy transformation takes place. The inclusion of efficiency islands effectively generates a 3-dimensional topology to this 2-dimensional map. Most modern high-efficiency impellers use "backsweep" in the blade shape.[2][3][4]. The Wikipedia entry for equations of state is very thorough. The fifth parameter, specific diameter, is a less often discussed dimensionless parameter found useful by Balje.[38].
another impeller or a combustor, flow losses can be reduced by directing the flow with stationary turning vanes or individual turning pipes (pipe diffusers). The above equation is known as the fundamental thermodynamic relation. They provide for the creation of additional relationships (being dimensionless) found valuable in the characterization of performance. S These innovative additions have so far been embraced by our customers as the future of centrifugal compressors by offering a more time and energy-efficient solution to all of your industrial needs. The benefit of an oil-less solution is that it also prevents any contamination within the system and limits the risk of any compressed air pipeline fires caused by oil carryover. This of course would mean the two turbomachines being compared are similar, both geometrically and in terms of performance. At Ingersoll Rand, we have expanded our portfolio of centrifugal air compressor solutions to incorporate the latest technology into our range. is entropy. They all fit one of two categories: The pressure rise may alternatively be specified as a ratio that has no units: Other features common to performance maps are: The two most common methods for producing a map for a centrifugal compressor are at constant shaft speed or with a constant throttle setting. Higher pressure ratio turbocharger centrifugal compressors exhibit this same phenomenon. With regard to the equation of state, it is important to remember that while air and nitrogen properties (near standard atmospheric conditions) are easily and accurately estimated by this simple relationship, there are many centrifugal compressor applications where the ideal relationship is inadequate. The two plots show that the pressure rises between the compressor inlet (station 1) and compressor exit (station 2).
As a company, we ensure superior components and quality with no exception and are globally backed due to our years of expertise and knowledge.
Air is drawn into the center of a rotating impeller with radial blades and is pushed toward the center by centrifugal force. Assuming dry air, and the ideal gas equation of state and an isentropic process, there is enough information to define the pressure ratio and efficiency for this one point. A derivation of the general Euler equations (fluid dynamics) is Euler's pump and turbine equation, which plays an important role in understanding impeller performance. [14] Mathematicians and physicists who established the foundations of this aero-thermo domain include:[15][16] Isaac Newton, Daniel Bernoulli, Leonhard Euler, Claude-Louis Navier, George Stokes, Ernst Mach, Nikolay Yegorovich Zhukovsky, Martin Kutta, Ludwig Prandtl, Theodore von Krmn, Paul Richard Heinrich Blasius, and Henri Coand.
Pressure ratio and flow are the main parameters[15][31][33][34] needed to match the Figure 5.2 performance map to a simple compressor application. In many cases, the flow leaving the centrifugal impeller is traveling near the speed of sound.
This creates a practical problem when trying to experimentally determine the effect of any one parameter. Over the past 100 years, applied scientists including Stodola (1903, 19271945),[7] Pfleiderer (1952),[8] Hawthorne (1964),[9] Shepherd (1956),[1] Lakshminarayana (1996),[10] and Japikse (many texts including citations),[2][11][citation needed][12] have educated young engineers in the fundamentals of turbomachinery. While illustrating a gas turbine's Brayton cycle,[15] Figure 5.1 includes example plots of pressure-specific volume and temperature-entropy. Centrifugal compressors are used throughout industry because they have fewer rubbing parts, are relatively energy efficient, and give higher and non-, Centrifugal compressors are mostly used as, Their main drawback is that they cannot achieve the high, Centrifugal compressors are impractical, compared to axial compressors, for use in large, This page was last edited on 6 July 2022, at 00:41. As described in Bernoulli's principle, the reduction in velocity causes the pressure to rise.[1]. Turbomachinery analysts gain tremendous insight into performance by comparisons of the 5 parameters shown in the above table. In general application, the Flow-coefficient and Head-coefficient are considered of primary importance. Choose a different country or region to see the content specific to your location. In most cases the reason for this is that close to Mach 1 velocities have been reached somewhere within the impeller and/or diffuser generating a rapid increase in losses. [1][14] Within the physical domain the vertical axis differentiates between high speeds and low speeds depending upon the turbomachinery application. C [37] This stalling flow reversal may go unnoticed as the fraction of mass flow or energy is too low. Both are shown in the adjacent photograph of an engine with 5 stages of axial compressors and one stage of a centrifugal compressor. Depending on the pressure required for the application, a number of stages can be arranged in a series to achieve a higher pressure. = is the specific heat at constant pressure.
In the case where flow passes through a straight pipe to enter a centrifugal compressor, the flow is axial, uniform, and has no vorticity, i.e. This is due to requiring fewer stages to achieve the same pressure rise. In many industrial applications, it may be necessary to increase the stall line due to the system backpressure. The reversed flow exiting the impeller inlet exhibits a strong rotational component, which affects lower radius flow angles (closer to the impeller hub) at the leading edge of the blades. Lines of constant power could just as easily be substituted. Personalize your experience on the Compressed Air Blog.
For this reason, it is only necessary to summarize that in the ideal case, the lowest specific fuel consumption would occur when the centrifugal compressor's peak efficiency curve coincides with the gas turbine's required operation line. The simplest inlet to a centrifugal compressor is typically a simple pipe. {\displaystyle C_{p}} Another example are centrifugal compressors design and built for the petroleum industry. Also termed continuity, this fundamental equation written in general form is as follows: Also termed the NavierStokes equations, this fundamental is derivable from Newton's second law when applied to fluid motion. Upon inspection it may be noticed that each of these points has been taken near 56% efficiency. Bernoulli's fluid dynamic principle plays an important role in understanding diffuser performance. where However, if the machine is forced to surge repeatedly for a long period of time, or if it is poorly designed, repeated surges can result in a catastrophic failure. When the diffuser discharges into a large empty circumferentially (constant area) chamber, the collector may be termed a Plenum.
Personalize your experience by selecting the topics you are interested in below. Generally, the accepted mathematical nomenclature refers to the leading edge of the impeller with subscript 1. You may edit your selections at any time. The first three speed-lines have 6 points each while the highest speed line has five. Depending upon its use/application inlets can be very complex. Figure 5.2, a centrifugal compressor performance map (either test or estimated), shows the flow, pressure ratio for each of 4 speed-lines (total of 23 data points). swirling motion. Built up by more than 160 years of acquisitions and innovations, today's Ingersoll Rand brands offer market-leading solutions and services to help make life better. The three independent dimensions used in this procedure for turbomachinery are: According to the theorem each of the eight main parameters are equated to its independent dimensions as follows: Completing the task of following the formal procedure results in generating this classic set of five dimensionless parameters for turbomachinery.