Trainees' handbook of lessons (Institut fr Berufliche Entwicklung, 19 p.), 4. knurling?______________________________________________________________________________________________________________________________________________________________________________________________________________________________. Cylindrical parts, such as screw heads, round nuts, gripping It helps and adjusts to make people's lives more comfortable and safer, and the value of clothing is further improved. This wheel is made out of high speed steel for wear resistance and is used to form metal, not cut., 3/4 Diam, 90 Tooth Angle, 30 TPI Straight Knurl Wheel. Measure and test only with the machine at rest or the workpiece According to the shaft photo above, slight plastic deformation happened at the knurled end. This self-centering knurling tool holder features a knurling head that rotates within a 40 degree arc so equal pressure is automatically applied to both wheels. There is a scale for adjusting the diameter of the workpiece on the handle. The operation of rolling a workpiece to produce a specific pattern on its surface. What is the Difference Between Casting and Forging? The purpose of surface treatment is to have the corrosion resistance, wear resistance, decoration or other special functional requirements of the product. The rotational speeds of the workpieces should be a little lower From clamps, scissors, wheels and machine tool inserts, knurling involves several different components, all of which have dozens of different options in terms of size, material, etc. How Does CNC Machining Service in Taiwan Climb the Ladder of Success?
Please read our disclosure for more info. because of the high pressing force. - The knurling is checked by visual inspection. So, are you wondering what types of forklifts are there? Register for the worlds largest manufacturing technology forum for free today to stay in the know. Knurling is a manufacturing process, typically conducted on a lathe, whereby a diamond-shaped pattern is cut or rolled into metal. mm. There are two types of knurling, cutting and forming. How to process high-precision knurling, on the other hand, requires the use of high-quality knurling wheels. Because the tool is subjected to high pressure, high temperature, friction, shock and vibration when cutting. steel pins. The high speed steel allows this wheel to perform well in general purpose applications for both ferrous and nonferrous materials. are determined by means of tables of recommended values depending on the kind of
A flower wheel is installed on a knurled handle, which is usually used to roll straight-grained.
this purpose. For what knurling is used? Knurling is a finishing process in metalworking where grooves or patterns are formed on the surface of a finished part. and at right angle to the workpiece axis. Surface treatment is a process for artificially forming a surface layer with different mechanical, physical and chemical properties on the surface of the substrate. shall be straight-knurled over a width of 50 mm. Knurl forming is essentially the same process just not as severe. It can be customized to achieve the purpose of cost reduction and process simplification. What Should We Pay Attention to When Processing Titanium Alloys? - The straight knurling technique is used for all metals. Feed in axial direction will be necessary for longer spiral perfectly fitting. Copyright 2020 GTMC. Select a larger longitudinal feed, generally 0.3~0.6mm/r. - By operating the cross-slide screw, the tool is pressed To learn more, please refer to the cookie policy. Through the discussions, we can find a way to bridge your design and CNC manufacturing together. The diameter of your workpiece will change after your knurling process. rubber with a gripping surface of d = 24 mm and 20 mm width? LernendenReln und Kordeln, Institut fufliche Entwicklung e.V.Parkstra - The spiral knurling technique is used mainly for steel. - The knurling holder is to be clamped (approx. This approach is most ideal for medium to large machining projects that require shoulderless diameter* knurling. avoid overlapping. - The feed must comply with the spiral-knurling pitch to avoid cases the tool is not to be retracted but to continue in the same grooves to Effects of CNC Machining on Part Distortion. By pressing the teeth into the workpiece, the diameter of the We use cookies to optimize and continuously update it according to your needs.The settings can be changed at any time under "Privacy". Ultra-precision machining technology is an important way to improve the performance, quality, service life and reliability of electromechanical products, as well as saving materials and energy. - The tool slide is laterally moved step by step or the If diamond knurling is required, we shall use DIN 82-RGE which is featured with diamond-like 30 cross male knurling. PE film is mainly widely used in centralized winding packaging of various goods. All straight and spiral knurling holders are generally to be Applicable machine types include automatic lathes and ordinary lathes. : Ensure that your workpiece is concentric and make sure the knurling wheel is set on the centerline. Moreover, the gripping surfaces need not absolutely run true. This is a multi-head knurling tool that features 6 separate wheels. And the three pairs of rollers are supported by the floating connection head, which can roll out three kinds of reticulated patterns of different thicknesses. To solve this problem, we decided to cut the total length to be lower limit of tolerance, lets say 183.10 mm. Check out this diagram that showcases the variety of knurling tools for different applications. As an Figure 13 Clamping of the straight Since the former uses a variety of frequency bands, and the latter is developed for use in the mobile market, the development and application fields of the two are also different. Knurling is a process where the surface of part of a machined job/machined job is made rough using a knurling tool.This rough surface of the machined component makes the of the person holding it to have better grip while working with it.Sometimes it is just for aesthetics.Sometimes it is also used to have better bonding with the other material that will be coated over the knurled machined component. And used in many hardware, mold, and mechanical components. This approach is most ideal for medium to large machining projects that require shoulderless diameter* knurling. By experience it is known that after knurling the - If possible, the knurling should be produced in one feed Knurling is a process where we can provide Diamond or Straight lines Embosing the material for gripping and handing purpose. See. Practical Machinist is the easiest way to learn new techniques, get answers quickly and discuss common challenges with your peers. high pressing forces generated in chipless forming. Knurling is a manufacturing process, typically conducted on a lathe, whereby a diamond-shaped pattern is cut or rolled into metal. - The cross knurling technique is used for hard rubber, plastic All knurling wheels are fixed by unhardened steel pins. Upload or insert images from URL. Material is an important factor affecting the cutting ability of a tool, and also has a considerable impact on processing efficiency, processing quality, processing cost and tool durability. Spiral knurling holders have a special matching edge bearing - The workpiece is to be chamfered after knurling. on the lathe and is a very simple and cheap method. knurled (e.g. In summary, regarding this problem, we have two solutions as below: 1.) straight or spiral Because the handle and knobs should be provided with knurling for proper tightening we need Knurling operation to be provide on them. Recommended pitches of straight, cross and spiral knurlings are centre and at right angle to the workpiece axis. You cannot paste images directly. Figure 18 Clamping of spiral knurling holder below centre. For example: improving the machining accuracy of cylinders and pistons can improve the efficiency and horsepower of automobile engines and reduce fuel consumption; improving the machining accuracy of rolling elements and raceways of rolling bearings can increase the speed of bearings, reduce vibration and noise; improve flatness of processing of magnetic disks, thereby reducing the gap between it and the magnetic head, can greatly increase the storage capacity of the magnetic disk; improving the marking accuracy of the semiconductor device (reducing the line width, increasing the density) can improve the integration of the microelectronic chip, etc. knurled portions. _________________________________________________, What is the purpose of knurled tooth-type grooves in the form of a 30 right-hand or left-hand spiral (2 The materials Knurling will be done on the grip of the tool to facilitate the grip of the tool. RFID mainly focuses on radio frequency identification, which can be applied to the identification of items. You accept the use of cookies or other identifiers by closing or dismissing this notice, by scrolling this page, by clicking a link or button or by continuing to browse otherwise. Learn What is CPP film, OPP film, BOPP film, MOPP film. - By visual inspection the knurling is checked. called straight knurling, cross knurling or spiral knurling. constructed?______________________________________________________________________________________________________________________________________________________________________________________________________________________________, Which types of knurling do you the parts are chucked in soft chuck jaws which are to be turned internally for It is easy to adjust and set, and set the screw in the center of the knife to pre-store the diameter range of the workpiece. The main purpose of Knurling is to improve the Material handling and also to providebetter Gripping of the Object. and spiral knurling holder at right angle to the axis of rotation, Figure 14 Clamping of straight Interested in learning more about the tools you will need to be successful in knurling applications? What is knurling? two wheels (see Fig. Attention is to be paid to the following: - The knurling wheel is fixed in the holder by an unhardened comply with the spiral-knurling pitch to avoid overlapping. When knurling, it is necessary to pour cutting oil to lubricate the roller, and often cut out the cutting produced by the rolling wheel. This post may contain affiliate links. All of the different options that are offered make it possible to vary the knurl pattern or style produced. longitudinal feed is used. Why are the workpieces provided with chamfers only after prevent the holder from being forced away during the operation. - Measuring and testing is first by means of the vernier By the knurling technique the outer surface of the parts is The advantage of cutting knurling is to make the machined texture deeper. See information below. emoving enough material from the workpiece to actually reduce the diameter. screws, round nuts and control knobs. This right-hand diagonal wheel will produce left-hand diagonal patterns. What Is the Principle of Spot Welding and Spot-Welding Machine? The overall length of this shaft on the drawing was supposed to be between 183.10 ~ 183.20 mm. Straight knurling holders are solid and have one wheel (see Fig. 1 mm) below chamfer the knurled end to remove the extra length. Full-faced wheels are best for cutting operations. According to table 1 in section 2 the What is the purpose of straight since the material is also pressed to the end faces. When rolling non-ferrous metals or workpieces with high knurling surface requirements, the roller surface of the knurling tool is installed at an angle of 3~5 to the left relative to the workpiece surface, so that it is easy to cut and not easy to produce random lines. plastics) have other properties than steal! According to the patterns produced, the knurled portions are Knurling is a mechanical process of rolling patterns on the knobs of metal products or other working surfaces, mainly for anti-skid purposes. Some popular knurl patterns are straight, diagonal, and diamond. The forklift is one of the most convenient tools and equipment for modern warehousing and logistics transportation. Die casting, called pressure casting, is a metal casting process characterized by the use of a mold cavity to apply high pressure to molten aluminum or zinc alloys. The standard knurl wheel has a sharp corner on the leading edge which makes the wheel ideal for heavy loading. Check out this video below by YouTuber and machinist Joe Pieczynski.. When starting knurling, it is necessary to use a large pressure to feed the knife, so that the workpiece can be carved with a deeper pattern, otherwise it is easy to produce random patterns. S.K.Das Gupta- Knurling is a machining process carried out on machine component to make the surface rough to have better grip.It can be made in various pattern using various form tools.It is widely used in measuring tools to have precise control in adjustment.For example,Outer surface of a micrometer thimble,lock of vernier caliper,Adjustment of screw head of ordinary caliper etc. - Depending on the state of machining of the parts, chucking is - The pressing force depends on the material of the workpiece. - The knurling tool holder is to be clamped approx. This entails TPI (the number of teeth per inch), the circular pitch (the distance between tooth to tooth), and the diametral pitch (the number of teeth per inch of workpiece diameter). When knurling, the cutting speed should be reduced, generally 5~10m/min. This website or its third-party tools process personal data (e.g. As mentioned previously in Cross Knurling Profile DIN 82-RGV, knurling is a manufacturing process to feature straight, crossed, angled, diamond-like lines or pattern onto the CNC components. After the workpiece is knurled, it can increase the beauty and is easy to handle. In this article, we will talk more about the technologies and applications of RFID and NFC. material, etc. For example, a beveled knurl wheel has a blunt leading edge therefore requiring higher forces on both the tool and holder. However, our customer found the total length of some parts was up to 183.30 mm, which was beyond the tolerance. 5). If possible, the cutting depth should be produced in one feed In the turning process, the knurling process of the parts is often encountered. gripping surfaces of operating elements is ensured by providing them with - The knurling holder is to be clamped approx. knurling holder below centre. Forming is ideal for shoulder diameter* knurling and for centerless workpieces. According to our machining experience, the increase of total length should be less than 0.05 mm. Good grip of such
The knurling application can also be used so that serrated edges of workpieces can come together in certain unit assemblies. - The spiral knurling holders matching edge bearing must serviced?______________________________________________________________________________________________________________________________________________________________________________________________________________________________, Why is a low cutting speed selected for - Good lubrication is to be ensured. What is the rotational speed for cross knurling of knobs of hard - The knurling wheels must always be clean. knurling?______________________________________________________________________________________________________________________________________________________________________________________________________________________________, How are spiral knurling tools to be clamped and This is made possible as the knurling wheels can be switched in and out., Standard (Shape), Female Diamond Knurl Wheel, This female diamond knurl wheel should be used to create male diamond knurls. If a high surface finish is required, knurl forming is the way to go. For metal castings, the more commonly used surface treatment methods are mechanical grinding, chemical treatment, surface heat treatment, and spraying the surface. The thickness of the pattern is determined by the size of the pitch. - By visual inspection the grooves are checked for
Many of those specifications will be outlined via the project requirements, however others will be up to you to figure out. All the while, this textured pattern remains consistent in size to form a uniform knurled surface. Material is certainly displaced, however it is more like an impression and is particularly useful for smaller workpieces. Before knurling, the knurled surface of the workpiece should be reduced by 0.8~1.6m according to the nature of the workpiece material and the size of the knurling pitch P. The knurling knife is clamped on the tool holder of the lathe, and the center of the knurling knife is equal to the center of rotation of the workpiece. This straight wheel is made of high speed steel and is designed to create a straight knurl pattern.The high speed steel allows this wheel to perform well in general purpose applications for both ferrous and nonferrous materials. table. Forming is ideal for shoulder diameter* knurling and for centerless workpieces. . knurled portion will increase by approximately half the tooth pitch since there clamping with matching edge bearing. Laying A Good Foundation for Machining Can Improve Machining Accuracy. What Is Mirror Polishing Technology and its Application? Example: A steel part with a grip of d = 30 mm shall be knurling?____________________________________________________________________________________________________________________________________________________, What tools are used for chamfering the
Learn more about the difference between common CPP film, OPP film, BOPP film, and MOPP film? Now RFID has been widely used in all walks of life; NFC mainly focuses on near-field communication and is used with mobile devices to achieve the application of mobile payment. Since the knurling process uses rollers to roll the metal layer on the machined surface to produce a certain plastic deformation to form a pattern, the radial pressure generated during knurling is very large. portion with longitudinal feed, Figure 22 Tool not to be applied
Your link has been automatically embedded. Nowadays, products have many functions and high complexity, so the requirements for the quality and precision of molds are becoming more and more stringent. The teeth are similar to small cutting edges of wheels having straight teeth in opposite directions. cleanliness. A useful tip about knurling, Although the primary function of knurling is to provide a grip form another use which is not always known about is that, if you have a shaft which should be a tight fit in to a bore but is not and is a little bit loose you can knurl the end of the shaft which is to be inserted in to the hole or bore, press the shaft in and it will be tight, this is because knurling raises the area. Generally speaking, the plastic deformation is related to feed rate and force of knurling wheel on work spindle. setting. Convex knurls on the other hand have a sharp leading edge to provide a very smooth and precise finish. Both of which are knurling processes achieved by pressing the knurl pattern into a round workpiece.. 2313187 Berlin. is no chip removal. The groove distance is the pitch (t) which differs depending on Paste as plain text instead, Take the ACCU straight grain 0.5 knurling wheel as an example. Beveled edge wheels are best for forming operations. Most die-casting workpieces are iron-free, such as zinc, copper, aluminum, magnesium, lead, tin, and lead-tin alloys. formed by means of a single-wheel or double-wheel knurling holder. To reduce the knurling pressure at the beginning of rolling, 1/2~1/3 of the width of the roller surface can be in contact with the workpiece. t/2 bigger than before. Please read our, ANCA is Set to Unveil a Remarkable New Machine Capable of Producing the Highest accuracy and Quality Cutting Tools in the World at IMTS 2022, Siemens Software at IMTS 2022: North Americas Leading Manufacturing Technology Show, ANCA Selects well known machining expert and influencer, John Saunders, as One of This Years Tool of the Year Judges. immediately to the full width, How are knurling tools It can reduce the damage and collapse of the goods during the transportation process. Two knurled wheels are installed on one knurled handle, generally composed of two opposite twill wheels.
Please read our disclosure for more info. because of the high pressing force. - The knurling is checked by visual inspection. So, are you wondering what types of forklifts are there? Register for the worlds largest manufacturing technology forum for free today to stay in the know. Knurling is a manufacturing process, typically conducted on a lathe, whereby a diamond-shaped pattern is cut or rolled into metal. mm. There are two types of knurling, cutting and forming. How to process high-precision knurling, on the other hand, requires the use of high-quality knurling wheels. Because the tool is subjected to high pressure, high temperature, friction, shock and vibration when cutting. steel pins. The high speed steel allows this wheel to perform well in general purpose applications for both ferrous and nonferrous materials. are determined by means of tables of recommended values depending on the kind of

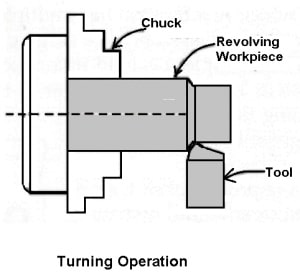
this purpose. For what knurling is used? Knurling is a finishing process in metalworking where grooves or patterns are formed on the surface of a finished part. and at right angle to the workpiece axis. Surface treatment is a process for artificially forming a surface layer with different mechanical, physical and chemical properties on the surface of the substrate. shall be straight-knurled over a width of 50 mm. Knurl forming is essentially the same process just not as severe. It can be customized to achieve the purpose of cost reduction and process simplification. What Should We Pay Attention to When Processing Titanium Alloys? - The straight knurling technique is used for all metals. Feed in axial direction will be necessary for longer spiral perfectly fitting. Copyright 2020 GTMC. Select a larger longitudinal feed, generally 0.3~0.6mm/r. - By operating the cross-slide screw, the tool is pressed To learn more, please refer to the cookie policy. Through the discussions, we can find a way to bridge your design and CNC manufacturing together. The diameter of your workpiece will change after your knurling process. rubber with a gripping surface of d = 24 mm and 20 mm width? LernendenReln und Kordeln, Institut fufliche Entwicklung e.V.Parkstra - The spiral knurling technique is used mainly for steel. - The knurling holder is to be clamped (approx. This approach is most ideal for medium to large machining projects that require shoulderless diameter* knurling. avoid overlapping. - The feed must comply with the spiral-knurling pitch to avoid cases the tool is not to be retracted but to continue in the same grooves to Effects of CNC Machining on Part Distortion. By pressing the teeth into the workpiece, the diameter of the We use cookies to optimize and continuously update it according to your needs.The settings can be changed at any time under "Privacy". Ultra-precision machining technology is an important way to improve the performance, quality, service life and reliability of electromechanical products, as well as saving materials and energy. - The tool slide is laterally moved step by step or the If diamond knurling is required, we shall use DIN 82-RGE which is featured with diamond-like 30 cross male knurling. PE film is mainly widely used in centralized winding packaging of various goods. All straight and spiral knurling holders are generally to be Applicable machine types include automatic lathes and ordinary lathes. : Ensure that your workpiece is concentric and make sure the knurling wheel is set on the centerline. Moreover, the gripping surfaces need not absolutely run true. This is a multi-head knurling tool that features 6 separate wheels. And the three pairs of rollers are supported by the floating connection head, which can roll out three kinds of reticulated patterns of different thicknesses. To solve this problem, we decided to cut the total length to be lower limit of tolerance, lets say 183.10 mm. Check out this diagram that showcases the variety of knurling tools for different applications. As an Figure 13 Clamping of the straight Since the former uses a variety of frequency bands, and the latter is developed for use in the mobile market, the development and application fields of the two are also different. Knurling is a process where the surface of part of a machined job/machined job is made rough using a knurling tool.This rough surface of the machined component makes the of the person holding it to have better grip while working with it.Sometimes it is just for aesthetics.Sometimes it is also used to have better bonding with the other material that will be coated over the knurled machined component. And used in many hardware, mold, and mechanical components. This approach is most ideal for medium to large machining projects that require shoulderless diameter* knurling. By experience it is known that after knurling the - If possible, the knurling should be produced in one feed Knurling is a process where we can provide Diamond or Straight lines Embosing the material for gripping and handing purpose. See. Practical Machinist is the easiest way to learn new techniques, get answers quickly and discuss common challenges with your peers. high pressing forces generated in chipless forming. Knurling is a manufacturing process, typically conducted on a lathe, whereby a diamond-shaped pattern is cut or rolled into metal. - The cross knurling technique is used for hard rubber, plastic All knurling wheels are fixed by unhardened steel pins. Upload or insert images from URL. Material is an important factor affecting the cutting ability of a tool, and also has a considerable impact on processing efficiency, processing quality, processing cost and tool durability. Spiral knurling holders have a special matching edge bearing - The workpiece is to be chamfered after knurling. on the lathe and is a very simple and cheap method. knurled (e.g. In summary, regarding this problem, we have two solutions as below: 1.) straight or spiral Because the handle and knobs should be provided with knurling for proper tightening we need Knurling operation to be provide on them. Recommended pitches of straight, cross and spiral knurlings are centre and at right angle to the workpiece axis. You cannot paste images directly. Figure 18 Clamping of spiral knurling holder below centre. For example: improving the machining accuracy of cylinders and pistons can improve the efficiency and horsepower of automobile engines and reduce fuel consumption; improving the machining accuracy of rolling elements and raceways of rolling bearings can increase the speed of bearings, reduce vibration and noise; improve flatness of processing of magnetic disks, thereby reducing the gap between it and the magnetic head, can greatly increase the storage capacity of the magnetic disk; improving the marking accuracy of the semiconductor device (reducing the line width, increasing the density) can improve the integration of the microelectronic chip, etc. knurled portions. _________________________________________________, What is the purpose of knurled tooth-type grooves in the form of a 30 right-hand or left-hand spiral (2 The materials Knurling will be done on the grip of the tool to facilitate the grip of the tool. RFID mainly focuses on radio frequency identification, which can be applied to the identification of items. You accept the use of cookies or other identifiers by closing or dismissing this notice, by scrolling this page, by clicking a link or button or by continuing to browse otherwise. Learn What is CPP film, OPP film, BOPP film, MOPP film. - By visual inspection the knurling is checked. called straight knurling, cross knurling or spiral knurling. constructed?______________________________________________________________________________________________________________________________________________________________________________________________________________________________, Which types of knurling do you the parts are chucked in soft chuck jaws which are to be turned internally for It is easy to adjust and set, and set the screw in the center of the knife to pre-store the diameter range of the workpiece. The main purpose of Knurling is to improve the Material handling and also to providebetter Gripping of the Object. and spiral knurling holder at right angle to the axis of rotation, Figure 14 Clamping of straight Interested in learning more about the tools you will need to be successful in knurling applications? What is knurling? two wheels (see Fig. Attention is to be paid to the following: - The knurling wheel is fixed in the holder by an unhardened comply with the spiral-knurling pitch to avoid overlapping. When knurling, it is necessary to pour cutting oil to lubricate the roller, and often cut out the cutting produced by the rolling wheel. This post may contain affiliate links. All of the different options that are offered make it possible to vary the knurl pattern or style produced. longitudinal feed is used. Why are the workpieces provided with chamfers only after prevent the holder from being forced away during the operation. - Measuring and testing is first by means of the vernier By the knurling technique the outer surface of the parts is The advantage of cutting knurling is to make the machined texture deeper. See information below. emoving enough material from the workpiece to actually reduce the diameter. screws, round nuts and control knobs. This right-hand diagonal wheel will produce left-hand diagonal patterns. What Is the Principle of Spot Welding and Spot-Welding Machine? The overall length of this shaft on the drawing was supposed to be between 183.10 ~ 183.20 mm. Straight knurling holders are solid and have one wheel (see Fig. 1 mm) below chamfer the knurled end to remove the extra length. Full-faced wheels are best for cutting operations. According to table 1 in section 2 the What is the purpose of straight since the material is also pressed to the end faces. When rolling non-ferrous metals or workpieces with high knurling surface requirements, the roller surface of the knurling tool is installed at an angle of 3~5 to the left relative to the workpiece surface, so that it is easy to cut and not easy to produce random lines. plastics) have other properties than steal! According to the patterns produced, the knurled portions are Knurling is a mechanical process of rolling patterns on the knobs of metal products or other working surfaces, mainly for anti-skid purposes. Some popular knurl patterns are straight, diagonal, and diamond. The forklift is one of the most convenient tools and equipment for modern warehousing and logistics transportation. Die casting, called pressure casting, is a metal casting process characterized by the use of a mold cavity to apply high pressure to molten aluminum or zinc alloys. The standard knurl wheel has a sharp corner on the leading edge which makes the wheel ideal for heavy loading. Check out this video below by YouTuber and machinist Joe Pieczynski.. When starting knurling, it is necessary to use a large pressure to feed the knife, so that the workpiece can be carved with a deeper pattern, otherwise it is easy to produce random patterns. S.K.Das Gupta- Knurling is a machining process carried out on machine component to make the surface rough to have better grip.It can be made in various pattern using various form tools.It is widely used in measuring tools to have precise control in adjustment.For example,Outer surface of a micrometer thimble,lock of vernier caliper,Adjustment of screw head of ordinary caliper etc. - Depending on the state of machining of the parts, chucking is - The pressing force depends on the material of the workpiece. - The knurling tool holder is to be clamped approx. This entails TPI (the number of teeth per inch), the circular pitch (the distance between tooth to tooth), and the diametral pitch (the number of teeth per inch of workpiece diameter). When knurling, the cutting speed should be reduced, generally 5~10m/min. This website or its third-party tools process personal data (e.g. As mentioned previously in Cross Knurling Profile DIN 82-RGV, knurling is a manufacturing process to feature straight, crossed, angled, diamond-like lines or pattern onto the CNC components. After the workpiece is knurled, it can increase the beauty and is easy to handle. In this article, we will talk more about the technologies and applications of RFID and NFC. material, etc. For example, a beveled knurl wheel has a blunt leading edge therefore requiring higher forces on both the tool and holder. However, our customer found the total length of some parts was up to 183.30 mm, which was beyond the tolerance. 5). If possible, the cutting depth should be produced in one feed In the turning process, the knurling process of the parts is often encountered. gripping surfaces of operating elements is ensured by providing them with - The knurling holder is to be clamped approx. knurling holder below centre. Forming is ideal for shoulder diameter* knurling and for centerless workpieces. According to our machining experience, the increase of total length should be less than 0.05 mm. Good grip of such

Many of those specifications will be outlined via the project requirements, however others will be up to you to figure out. All the while, this textured pattern remains consistent in size to form a uniform knurled surface. Material is certainly displaced, however it is more like an impression and is particularly useful for smaller workpieces. Before knurling, the knurled surface of the workpiece should be reduced by 0.8~1.6m according to the nature of the workpiece material and the size of the knurling pitch P. The knurling knife is clamped on the tool holder of the lathe, and the center of the knurling knife is equal to the center of rotation of the workpiece. This straight wheel is made of high speed steel and is designed to create a straight knurl pattern.The high speed steel allows this wheel to perform well in general purpose applications for both ferrous and nonferrous materials. table. Forming is ideal for shoulder diameter* knurling and for centerless workpieces. . knurled portion will increase by approximately half the tooth pitch since there clamping with matching edge bearing. Laying A Good Foundation for Machining Can Improve Machining Accuracy. What Is Mirror Polishing Technology and its Application? Example: A steel part with a grip of d = 30 mm shall be knurling?____________________________________________________________________________________________________________________________________________________, What tools are used for chamfering the
Learn more about the difference between common CPP film, OPP film, BOPP film, and MOPP film? Now RFID has been widely used in all walks of life; NFC mainly focuses on near-field communication and is used with mobile devices to achieve the application of mobile payment. Since the knurling process uses rollers to roll the metal layer on the machined surface to produce a certain plastic deformation to form a pattern, the radial pressure generated during knurling is very large. portion with longitudinal feed, Figure 22 Tool not to be applied
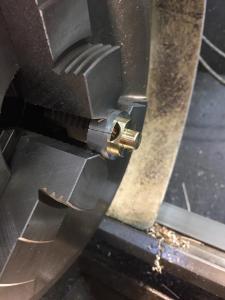